A process suitable for simultaneous separation of copper smelting electric furnace slag and converter slag
A process method and electric furnace slag technology, which can be used in flotation, solid separation and other directions, can solve the problems of high cost and no economic benefits, and achieve the effect of reducing production costs.
- Summary
- Abstract
- Description
- Claims
- Application Information
AI Technical Summary
Problems solved by technology
Method used
Image
Examples
Embodiment 1
[0011] Embodiment 1: as figure 1 , figure 2 As shown, if the raw ore is electric furnace slag, it will enter the two-stage continuous grinding-flotation process; if the raw ore is converter slag, it will enter the two-stage grinding-two-stage flotation process; the two-stage continuous grinding-flotation The process includes sending the raw ore into the ore grinding machine M1 for primary grinding, entering the ore grinding machine M2 through the valve V1 for secondary grinding, and then entering the primary roughing flotation machine C1, valve V5, and secondary roughing through the valve V3 in sequence. Flotation machine C2, scavenging flotation machines S1, S2, S3 and selection flotation machines J1, J2, J3, after two times of roughing, three times of cleaning and three times of scavenging, the tailings are selected and the scavenging concentrate Sequentially return to the previous operation to obtain the final concentrate and tailings products; such as figure 1 , image...
Embodiment 2
[0021] Preferred embodiment 2: if the raw ore is electric furnace slag, then enter into two-stage continuous grinding-flotation process; if the raw ore is converter slag, then enter into two-stage grinding-two-stage flotation process; the two-stage continuous grinding- The flotation process includes sending the raw ore into the ore grinding machine M1 for primary grinding, entering the ore grinding machine M2 through the valve V1 for secondary grinding, and then entering the primary roughing flotation machine C1, valve V5, and secondary grinding through the valve V3 in sequence. Roughing flotation machine C2, scavenging flotation machines S1, S2, S3 and fine flotation machines J1, J2, J3, after two roughings, three cleanings and three cleanings, tailings cleaning, cleaning The concentrate returns to the previous operation in order to obtain the final concentrate and tailings products. The sodium bicarbonate of 70g / t parts by weight of water glass and 140g / t parts of sodium bica...
Embodiment 3
[0022]Preferred embodiment 3: if the raw ore is electric furnace slag, then enter into two-stage continuous grinding-flotation process, if the raw ore is converter slag, then enter into two-stage grinding-two-stage flotation process; the two-stage continuous grinding- The flotation process includes sending the raw ore into the ore grinding machine M1 for primary grinding, entering the ore grinding machine M2 through the valve V1 for secondary grinding, and then entering the primary roughing flotation machine C1, valve V5, and secondary grinding through the valve V3 in sequence. Roughing flotation machine C2, scavenging flotation machines S1, S2, S3 and fine flotation machines J1, J2, J3, after two roughings, three cleanings and three cleanings, tailings cleaning, cleaning The concentrate returns to the previous operation in order to obtain the final concentrate and tailings products. The first roughing adds 80g / t weight of water glass and 160g / t weight of sodium bicarbonate as ...
PUM
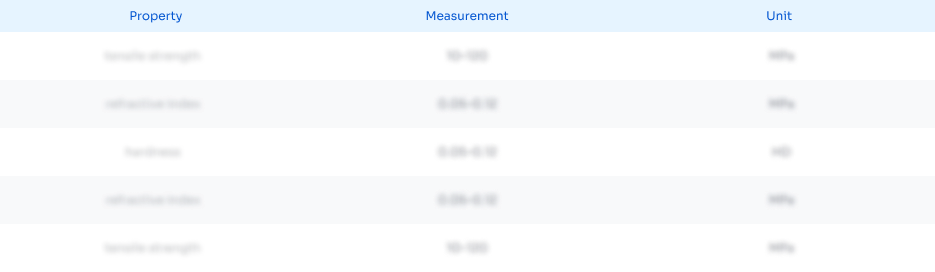
Abstract
Description
Claims
Application Information

- Generate Ideas
- Intellectual Property
- Life Sciences
- Materials
- Tech Scout
- Unparalleled Data Quality
- Higher Quality Content
- 60% Fewer Hallucinations
Browse by: Latest US Patents, China's latest patents, Technical Efficacy Thesaurus, Application Domain, Technology Topic, Popular Technical Reports.
© 2025 PatSnap. All rights reserved.Legal|Privacy policy|Modern Slavery Act Transparency Statement|Sitemap|About US| Contact US: help@patsnap.com