A kind of welding method of max phase ceramic material
A technology of ceramic materials and welding methods, applied in welding equipment, resistance welding equipment, metal processing equipment, etc., can solve the problems of high equipment requirements, reduced efficiency, increased costs, etc., achieve high flexibility, enhance bending strength, and weld short cycle effect
- Summary
- Abstract
- Description
- Claims
- Application Information
AI Technical Summary
Problems solved by technology
Method used
Image
Examples
Embodiment 1
[0031] In this embodiment, both the first MAX phase ceramic material 1 and the second MAX phase ceramic material 2 are Ti 3 SiC 2 bulk material, for two Ti 3 SiC 2 The material is welded, the specific method is as follows:
[0032] (1) Put two pieces of Ti 3 SiC 2 After grinding and polishing the surfaces to be welded of materials 1 and 2, wash them with acetone and deionized water;
[0033] (2) if figure 1 As shown, the two Ti 3 SiC 2 The surfaces of the materials to be welded are aligned and contacted together, and the two Ti 3 SiC 2 The materials are respectively connected with the graphite upper electrode 3 and the graphite lower electrode 4, the power supply 5, the graphite upper electrode 3, two pieces of Ti 3 SiC 2 Materials 1 and 2 and graphite lower electrode 4 form a closed loop;
[0034](3) Through graphite electrodes 3 and 4 on two pieces of Ti 3 SiC 2 Apply a pressure of 13MPa on materials 1 and 2;
[0035] (4) Apply current to the whole system, Ti ...
Embodiment 2
[0039] In this embodiment, both the first MAX phase ceramic material 1 and the second MAX phase ceramic material 2 are Ti 3 SiC 2 bulk material, for two Ti 3 SiC 2 The material is welded, the specific method is basically the same as that described in Example 1, the difference is that in step (3), graphite electrodes 3 and 4 are used on two Ti 3 SiC 2 A pressure of 1 MPa is applied to materials 1 and 2; in step (4), the current intensity is loaded to 2.2KA and the current is stopped; the welding process takes 7 minutes.
[0040] Figure 4 is the ti 3 SiC 2 Scanning electron microscope (SEM) photograph of the interface cross-section of the material after welding. It can be seen from the figure that the two Ti 3 SiC 2 The material is connected as one, there is no weld seam at the interface, and there is no interface.
Embodiment 3
[0042] In this embodiment, both the first MAX phase ceramic material 1 and the second MAX phase ceramic material 2 are Ti 3 SiC 2 bulk material, for two Ti 3 SiC 2 The material is welded, the specific method is basically the same as that described in Example 1, the difference is that in step (3), graphite electrodes 3 and 4 are used on two Ti 3 SiC 2 A pressure of 5 MPa is applied to materials 1 and 2; in step (4), the current is stopped after the current intensity reaches 2.5KA; the welding process takes 6 minutes.
[0043] Figure 5 is the ti 3 SiC 2 Scanning electron microscope (SEM) photograph of the interface cross-section of the material after welding. It can be seen from the figure that the two Ti 3 SiC 2 The material is connected as one, there is no weld seam at the interface, and there is no interface.
PUM
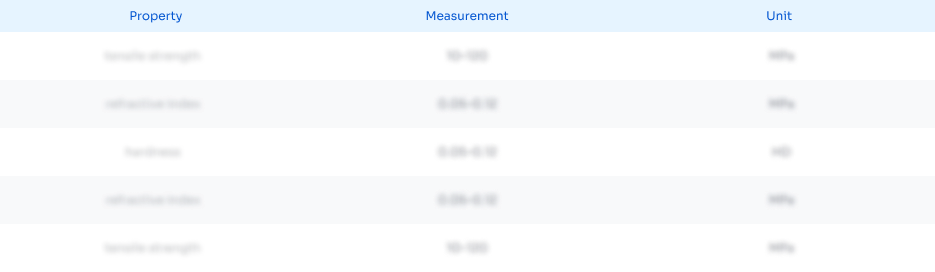
Abstract
Description
Claims
Application Information

- Generate Ideas
- Intellectual Property
- Life Sciences
- Materials
- Tech Scout
- Unparalleled Data Quality
- Higher Quality Content
- 60% Fewer Hallucinations
Browse by: Latest US Patents, China's latest patents, Technical Efficacy Thesaurus, Application Domain, Technology Topic, Popular Technical Reports.
© 2025 PatSnap. All rights reserved.Legal|Privacy policy|Modern Slavery Act Transparency Statement|Sitemap|About US| Contact US: help@patsnap.com