Lost foam casting coating for gray cast iron and preparation method of lost foam casting coating
A technology of lost foam and gray cast iron, which is applied to casting molding equipment, coatings, casting molds, etc. It can solve the problems of sand sticking in castings, and achieve the effect of cost reduction and cost increase
- Summary
- Abstract
- Description
- Claims
- Application Information
AI Technical Summary
Problems solved by technology
Method used
Image
Examples
Embodiment 1
[0033] Example 1 A lost foam coating for gray cast iron and its preparation method
[0034] A lost foam coating for gray cast iron, which comprises the following raw materials:
[0035] Quartz powder 84 kg, mica powder 6 kg, vermiculite powder 2 kg, attapulgite 4 kg,
[0036] Recover 4 kg of pellet dust, 0.5 kg of latex powder, 0.8 kg of dextrin,
[0037] Carboxymethylcellulose sodium 1.0 kg, sodium bentonite 1.5 kg, sodium hexametaphosphate 0.5 kg,
[0038] Sodium tripolyphosphate 1.0 kg, organosilicon 0.1 kg, zinc oxide 0.02 kg, sodium benzoate 0.06 kg.
[0039] Its preparation method is carried out according to the following sequence of steps:
[0040] (1) Preparation of aggregate: First, add quartz powder, mica powder, vermiculite powder, attapulgite, and recovered dust into the mixing elevator in sequence, and carry out automatic lifting and stirring three times. The time for each automatic lifting and stirring is 12 minutes , and finally aggregates are obtained.
...
Embodiment 2-6
[0044] Example 2-6 Lost foam coating for gray cast iron and preparation method thereof
[0045] Examples 2-6 are respectively a kind of lost foam coating for gray cast iron and its preparation method, which are similar to the raw materials and preparation method of Example 1, except that the amount of raw materials and the preparation parameters involved in the preparation method are different. The details are shown in the following table:
[0046] The raw material composition and the technical parameters involved in the preparation method of the aggregate in the table 1 embodiment 2-6
[0047]
[0048] The preparation parameters involved in the consumption of raw materials and preparation method in table 2 embodiment 2-6
[0049]
[0050] The lost foam coatings for gray cast iron prepared in Examples 2-6 can make high-temperature gas discharge from the coating rapidly and almost invariably when pouring thick-walled castings, and reduce carbon black and pore defects t...
PUM
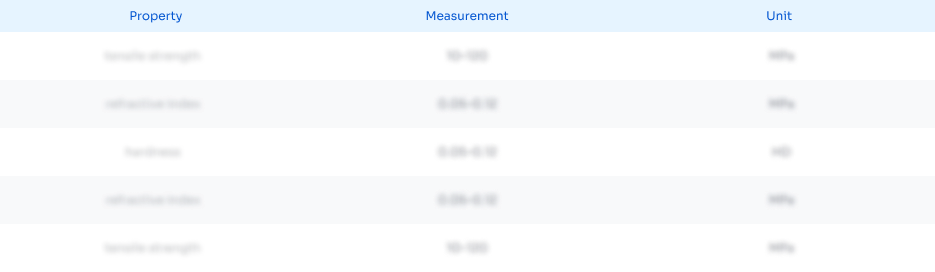
Abstract
Description
Claims
Application Information

- Generate Ideas
- Intellectual Property
- Life Sciences
- Materials
- Tech Scout
- Unparalleled Data Quality
- Higher Quality Content
- 60% Fewer Hallucinations
Browse by: Latest US Patents, China's latest patents, Technical Efficacy Thesaurus, Application Domain, Technology Topic, Popular Technical Reports.
© 2025 PatSnap. All rights reserved.Legal|Privacy policy|Modern Slavery Act Transparency Statement|Sitemap|About US| Contact US: help@patsnap.com