A kind of lightweight composite material momentum flywheel for satellite and its preparation method
A technology of composite materials and flywheels, which is applied in the direction of aerospace vehicle guides, etc., can solve the problems that are difficult to meet the requirements for mass use of lightweight satellite platforms, increase the cycle and cost of flywheels, and affect the performance of flywheel dynamic balance, etc., to achieve increased balance and stability High performance, meeting attitude control requirements, and excellent damping performance
- Summary
- Abstract
- Description
- Claims
- Application Information
AI Technical Summary
Problems solved by technology
Method used
Image
Examples
Embodiment 1
[0043] This embodiment combines figure 1 , 2 , 3 for further explanation, the satellite that the present embodiment relates to is used the lightweight composite material momentum flywheel, comprises wheel hub 1, wheel spoke 2, wheel rim 3 successively (see figure 1 ), the middle of the hub 1 is provided with a middle hole 4, and the spokes include outer spokes 5, spokes 6, and inner spokes 7; the material of the hub is 7075 aluminum alloy (see figure 2 ), the outer circumference is provided with a connecting groove, the groove is trapezoidal, and the inclination angle of the side is 15°; the spoke (see image 3 ) is a carbon fiber composite material, and the inner spokes and rectangular spokes in contact with the hub are laid layer by layer with integrally cut T300 / epoxy resin prepreg cloth, and the laying angle is [0 / 45 / 45 / 90] cycle, the outer The outer spoke ring in contact with the rim is wound in full axial direction with T700 / epoxy resin prepreg; the rim (see Figure ...
Embodiment 2
[0053] This embodiment provides a lightweight composite momentum flywheel for satellites and its preparation method. The technical solution is a preferred example of implementation 1. The only improvements are:
[0054] Step 3: The inner surface of the wheel rim is subjected to sandblasting and roughening treatment with high-pressure fine sand: the size of the fine sand is 0-100 mesh, the sandblasting pressure is 0.8MPa, and the spraying time is 20 minutes;
[0055] In step 4, heat the mold to about 120°C for 0.5h, slowly pressurize to 0.3MPa, release the pressure, then increase the pressure to 1.2MPa, and at the same time raise the temperature to 180°C, and cure for 6h, so that the aluminum alloy hub, spoke and The rim is co-solidified into one.
[0056] The number of spokes of the prepared flywheel is 8; the length and width of the vertical section of the spokes are 20mm and 10mm respectively; The ratio between them is 4:5:6.
Embodiment 3
[0058] This embodiment provides a lightweight composite momentum flywheel for satellites and its preparation method. The technical solution is a preferred example of implementation 1. The only improvements are:
[0059] Step 3: The inner surface of the wheel rim is subjected to sandblasting and roughening treatment with high-pressure fine sand: the size of the fine sand is 0-100 mesh, the sandblasting pressure is 0.5MPa, and the spraying time is 15 minutes;
[0060] In step 4, heat the mold to about 100°C for 0.5h, slowly pressurize to 0.2MPa, release the pressure, then increase the pressure to 1MPa, and at the same time raise the temperature to 180°C, and cure for 4.5h, so that the hub, spoke and rim co-cured into one.
[0061] The number of spokes of the prepared flywheel is 10; the length and width of the vertical section of the spokes are 10mm and 10mm respectively; The ratio between them is 4:5:6.
PUM
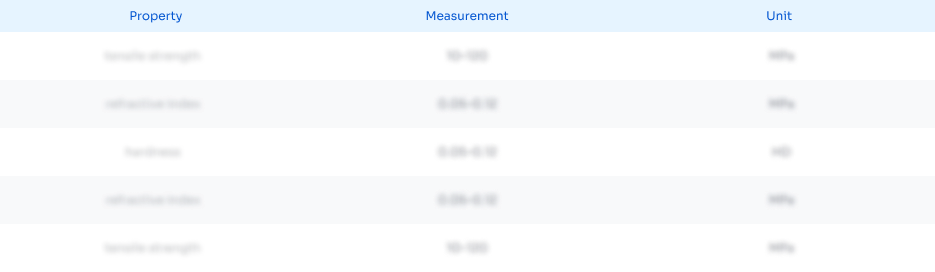
Abstract
Description
Claims
Application Information

- R&D
- Intellectual Property
- Life Sciences
- Materials
- Tech Scout
- Unparalleled Data Quality
- Higher Quality Content
- 60% Fewer Hallucinations
Browse by: Latest US Patents, China's latest patents, Technical Efficacy Thesaurus, Application Domain, Technology Topic, Popular Technical Reports.
© 2025 PatSnap. All rights reserved.Legal|Privacy policy|Modern Slavery Act Transparency Statement|Sitemap|About US| Contact US: help@patsnap.com