Design method of sensorless sliding mode observer for electrical vehicle motor
A technology of sliding mode observer and electric vehicle, which is applied in the direction of motor generator control, electronic commutation motor control, control of electromechanical brake, etc., and can solve problems such as system instability, affecting control system accuracy, system chattering, etc.
- Summary
- Abstract
- Description
- Claims
- Application Information
AI Technical Summary
Problems solved by technology
Method used
Image
Examples
Embodiment Construction
[0036] The technical solutions of the present invention will be described in detail below in conjunction with the accompanying drawings and specific embodiments.
[0037] The main process of the present invention is as figure 1 shown, including:
[0038] Step S1, using figure 1 The sensor of the shown motor hardware circuit collects the motor two-phase current i a i b ;
[0039] Step S2, calculate the component i of the stator current on the αβ axis α i β ;
[0040] In this step, the current state equation of the motor in the αβ coordinate system is:
[0041] di α dt = - R s L s i α + ...
PUM
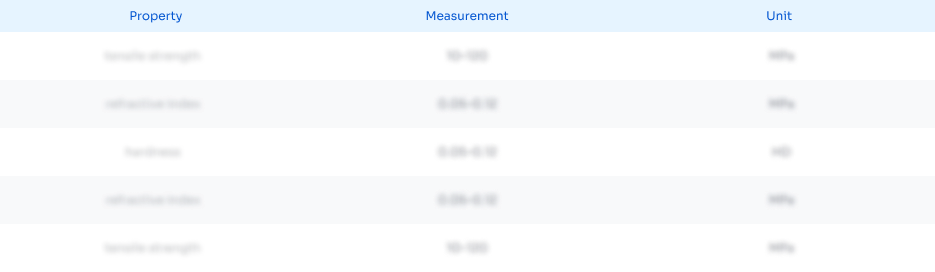
Abstract
Description
Claims
Application Information

- R&D
- Intellectual Property
- Life Sciences
- Materials
- Tech Scout
- Unparalleled Data Quality
- Higher Quality Content
- 60% Fewer Hallucinations
Browse by: Latest US Patents, China's latest patents, Technical Efficacy Thesaurus, Application Domain, Technology Topic, Popular Technical Reports.
© 2025 PatSnap. All rights reserved.Legal|Privacy policy|Modern Slavery Act Transparency Statement|Sitemap|About US| Contact US: help@patsnap.com