High-reliability electric-drive motor control method
An electric drive and motor control technology, applied in the direction of motor generator control, AC motor control, electronic commutation motor control, etc., can solve the problem of the increase of system bandwidth that affects the dynamic performance of the system, the poor adaptive ability of the speed PI controller, and the system Control poor reliability and other problems to achieve the effect of increasing self-adaptive ability and anti-disturbance ability, good tracking effect and improving reliability
- Summary
- Abstract
- Description
- Claims
- Application Information
AI Technical Summary
Problems solved by technology
Method used
Image
Examples
Embodiment Construction
[0018] Specific embodiments of the present invention will be described in detail below in conjunction with the accompanying drawings, so that those skilled in the art can better understand the present invention.
[0019] Such as figure 1 As shown, it is a specific implementation of a highly reliable electric drive motor control method according to the present invention, and its specific implementation steps are:
[0020] (1) Collect the current i of the motor through the Hall sensor a i b , and then pass it through the abc / dq converter to get the actual current value i in the d-q coordinate system d and i q ;
[0021] (2) The position signal θ of the motor is collected by the position detector, and the position signal is differentiated to obtain the feedback speed signal rotor mechanical angular velocity ω r ;
[0022] (3) The given rotational speed ω r * with the feedback speed ω r Send it to the fuzzy PR regulator for processing, and get the given current i with str...
PUM
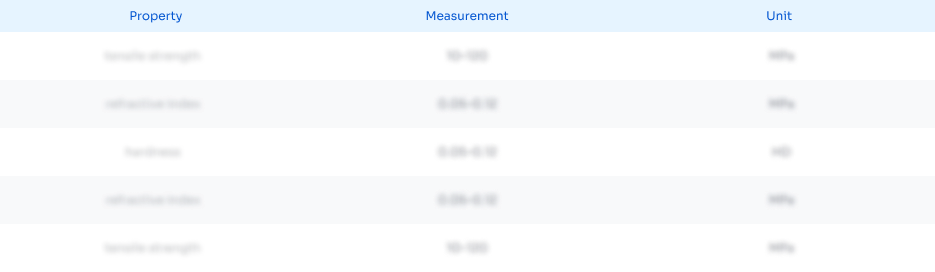
Abstract
Description
Claims
Application Information

- R&D
- Intellectual Property
- Life Sciences
- Materials
- Tech Scout
- Unparalleled Data Quality
- Higher Quality Content
- 60% Fewer Hallucinations
Browse by: Latest US Patents, China's latest patents, Technical Efficacy Thesaurus, Application Domain, Technology Topic, Popular Technical Reports.
© 2025 PatSnap. All rights reserved.Legal|Privacy policy|Modern Slavery Act Transparency Statement|Sitemap|About US| Contact US: help@patsnap.com