Surface conduction electron emission source structure and manufacturing method thereof
A technology for conduction electrons and electron emission, which is applied in the manufacture of thermionic cathodes, cathode ray tubes/electron beam tubes, circuits, etc. Low efficiency and other problems, to achieve the effect of low equipment requirements, improved field emission electron efficiency, and easy scattering
- Summary
- Abstract
- Description
- Claims
- Application Information
AI Technical Summary
Problems solved by technology
Method used
Image
Examples
Embodiment 1
[0049] see Pic 4-1 and Figure 4-2 , a surface conduction electron emission source structure with a raised center, including two device electrodes 150, a protruding dielectric 310 and an electron emission film 250 located in the middle of the electrode gap.
[0050] The process of making this structure is:
[0051] 1) Using magnetron sputtering or other methods to sputter several groups of metal electrodes 150 on the substrate 100 to form an electrode array, the thickness of the electrodes is 100-200 nm, and there is a gap of 8-20 μm between the electrodes;
[0052] 2) Sputter a layer of protruding dielectric 310 between the device electrodes 150 with a width of 2-5 μm, a length equivalent to that of the surface conduction electron emission film 250, and a thickness of 100-150 nm between the device electrodes 150 by means of magnetron sputtering;
[0053] 3) sputtering a surface conduction electron emission film 250 between the device electrodes 150 by means of magnetron sp...
Embodiment 2
[0056] see Figure 5-1 and Figure 5-2 , a surface conduction electron emission source structure with one side raised, the structure includes two device electrodes 150, one side is connected to the electrodes, a dielectric filling layer 300 and an electron emission film 250 filling part of the gap between the electrodes.
[0057] The process of making this structure is:
[0058] 1) Using magnetron sputtering or other methods to sputter several groups of metal electrodes 150 on the substrate 100 to form an electrode array, the thickness of the electrodes is 100-200 nm, and there is a gap of 8-20 μm between the electrodes;
[0059] 2) Use magnetron sputtering or other methods to sputter a dielectric filling layer 300 with a thickness equivalent to the thickness of the electrodes between the device electrodes 150, fill the dielectric filling layer 300 with a width of 4-8 μm, one side of which is connected to one end of the electrode, and the other side in the electrode gap.
...
Embodiment 3
[0063] see Figure 6-1 and Figure 6-2 , a surface conduction electron emission source structure with a filled middle pad, including two device electrodes 150 , a dielectric filling layer 300 , a protruding dielectric 310 and an electron emission film 250 .
[0064] During fabrication, the dielectric filling layer 300 is fabricated first, and then the protruding dielectric 310 is fabricated. The specific fabrication steps are as follows:
[0065] 1) Using magnetron sputtering or other methods to sputter several groups of metal electrodes 150 on the substrate 100 to form an electrode array, the thickness of the electrodes is 100-200 nm, and there is a gap of 8-20 μm between the electrodes;
[0066] 2) Sputtering a dielectric filling layer 300 with a thickness equivalent to the electrode thickness between the device electrodes 150 to fill the electrode gap by magnetron sputtering or other methods;
[0067] 3) sputtering a layer of protruding dielectric 310 between the device e...
PUM
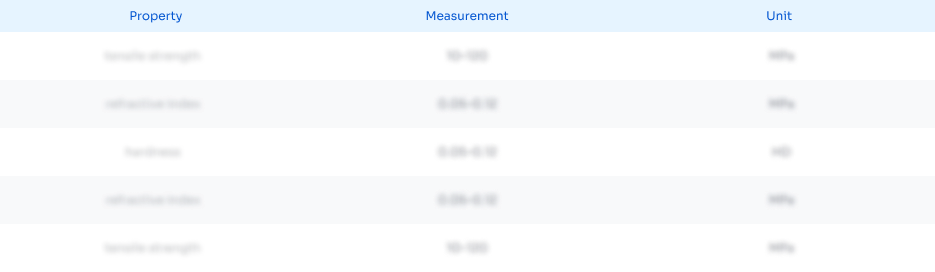
Abstract
Description
Claims
Application Information

- R&D
- Intellectual Property
- Life Sciences
- Materials
- Tech Scout
- Unparalleled Data Quality
- Higher Quality Content
- 60% Fewer Hallucinations
Browse by: Latest US Patents, China's latest patents, Technical Efficacy Thesaurus, Application Domain, Technology Topic, Popular Technical Reports.
© 2025 PatSnap. All rights reserved.Legal|Privacy policy|Modern Slavery Act Transparency Statement|Sitemap|About US| Contact US: help@patsnap.com