Model verification method for prediction model of underwater ship corrosion-related static magnetic field
A static magnetic field and predictive model technology, which is applied in electrostatic field measurement, weather resistance/light resistance/corrosion resistance, measuring devices, etc., can solve problems such as difficult magnetic field distinction, unpredictable model verification, etc.
- Summary
- Abstract
- Description
- Claims
- Application Information
AI Technical Summary
Problems solved by technology
Method used
Image
Examples
Embodiment Construction
[0038] The present invention will be further described below in conjunction with accompanying drawing of description and specific embodiment:
[0039] The invention provides a method for checking the model of a ship's underwater corrosion-related static magnetic field prediction model, which is characterized in that it includes the following steps:
[0040] first step, such as figure 1 As shown, the seawater and marine environment are simulated in the laboratory, and the conductivity of the self-prepared simulated seawater is σ 1 =0.0814S m -1 . Build the ship model 7 and its ICCP system according to the scale of 1:100. 20 measuring electrodes 8 are used, with a distance of 8 cm between them, arranged in an array to form a measuring array of electric field sensors, and arranged on a plane 50 cm below the water surface below the ship model 7 to measure the scalar potential distribution on the plane. The measuring electrode 8 is a 218-type Ag-AgCl reference electrode from Sh...
PUM
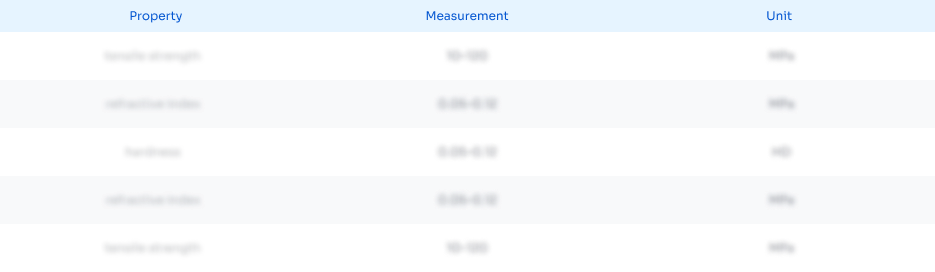
Abstract
Description
Claims
Application Information

- Generate Ideas
- Intellectual Property
- Life Sciences
- Materials
- Tech Scout
- Unparalleled Data Quality
- Higher Quality Content
- 60% Fewer Hallucinations
Browse by: Latest US Patents, China's latest patents, Technical Efficacy Thesaurus, Application Domain, Technology Topic, Popular Technical Reports.
© 2025 PatSnap. All rights reserved.Legal|Privacy policy|Modern Slavery Act Transparency Statement|Sitemap|About US| Contact US: help@patsnap.com