High-thermal-diffusion-coefficient high molecular material and preparation method thereof
A polymer material and diffusion coefficient technology, applied in the field of polymer materials and its preparation, can solve problems such as unsatisfactory, low thermal diffusivity, deviation of heat dissipation effect, etc., to improve heat conduction, improve interface performance, and reduce viscosity Effect
- Summary
- Abstract
- Description
- Claims
- Application Information
AI Technical Summary
Problems solved by technology
Method used
Examples
Embodiment 1
[0032] Example 1 According to the formula in Table 1, 5 different formula products (1#~5# in Table 1) were produced, and compared with the products produced by the formula (6#) without adding high thermal conductivity filler. Table 2 shows the physical property measurement results of 6 different products produced according to the formula in Table 1.
[0033] Table 1 Product formula table (unit: parts by weight)
[0034] .
[0035] The specific formula and preparation method adopted in the present embodiment are as follows:
[0036]1. Formula: matrix resin (translucent or opaque milky white granular polycaprolactam with a relative viscosity of 2.8), high thermal diffusion thermal conductivity filler (hexagonal boron nitride, thermal conductivity graphene, carbon nanotubes, spherical alumina by mass ratio 4: 1:1:15 for compounding), carbon fiber composite material (chopped carbon fiber with a length of 6-8um), toughening agent (SEBS grafted with maleic anhydride with a male...
Embodiment 2
[0047] Embodiment 2 adopts following formula and steps to realize the present invention:
[0048] 1. Formula: 60.5 parts of matrix resin (polyhexamethylene adipamide, acrylonitrile-butadiene-styrene copolymer), high thermal diffusion thermal conductivity filler (hexagonal boron nitride, thermal conductivity graphene, carbon nanotubes, spherical oxide Aluminum compounded according to the mass ratio of 5:1:2:12) 35.5 parts, carbon fiber composite material (microcrystalline graphite) 2 parts, toughening agent (maleic anhydride grafted POE) 8 parts, coupling agent (organic complex object coupling agent) 1 part, 0.5 parts of antioxidant 1098, 1 part of antioxidant 1076, 10 parts of other additives (5 parts of antistatic agent, 5 parts of lubricant);
[0049] 2. Preparation method:
[0050] (1) Put the high-thermal diffusion and heat-conducting filler into a high-speed mixer for high-speed mixing, and add 2% of its mass white mineral oil at the same time;
[0051] (2) Prepare a...
Embodiment 3
[0057] Embodiment 3 adopts following formula and steps to realize the present invention:
[0058] 1. Formula: 20 parts of matrix resin (industrial liquid crystal polymer, polypropylene), high thermal diffusion thermal conductivity filler (hexagonal boron nitride, thermal conductivity graphene, carbon nanotubes, magnesium oxide in a mass ratio of 4:1:1:15) 65 parts, carbon fiber composite material (microcrystalline graphite) 1 part, toughening agent (ethylene-vinyl acetate copolymer) 3 parts, coupling agent (aluminate coupling agent) 0.5 part, antioxidant 168 0.8 1.6 parts of antioxidant 1076, 2 parts of other additives (anti-dripping agent);
[0059] 2. Preparation method:
[0060] (1) Put the high-thermal diffusion and heat-conducting filler into a high-speed mixer for high-speed mixing, and add 1.5% of its mass white mineral oil at the same time;
[0061] (2) Prepare a water-absolute ethanol solution, the mass percentage of water in the solution is 6%; dissolve the couplin...
PUM
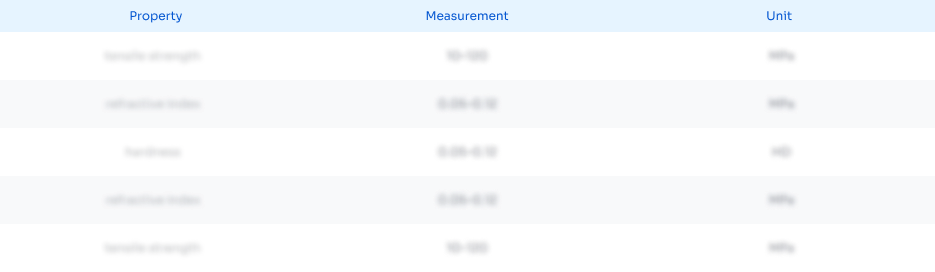
Abstract
Description
Claims
Application Information

- Generate Ideas
- Intellectual Property
- Life Sciences
- Materials
- Tech Scout
- Unparalleled Data Quality
- Higher Quality Content
- 60% Fewer Hallucinations
Browse by: Latest US Patents, China's latest patents, Technical Efficacy Thesaurus, Application Domain, Technology Topic, Popular Technical Reports.
© 2025 PatSnap. All rights reserved.Legal|Privacy policy|Modern Slavery Act Transparency Statement|Sitemap|About US| Contact US: help@patsnap.com