Rapid densification method of carbon/carbon composite material
A carbon composite material and composite material technology are applied in the field of rapid preparation of carbon/carbon composite materials to achieve the effect of improving densification efficiency
- Summary
- Abstract
- Description
- Claims
- Application Information
AI Technical Summary
Problems solved by technology
Method used
Image
Examples
Embodiment 1
[0038] (1) Set the initial density to 0.19g / cm 3 The carbon fiber full mesh felt is densified to 0.9g / cm by CVI 3 , control the pyrolytic carbon microstructure of the substrate to rough layer structure pyrolytic carbon; CVI process parameters are: temperature: 1180 °C; pressure: 15KPa; propylene flow rate: 6.0L / min; nitrogen flow rate: 9L / min; time: 50h.
[0039] (2) The carbon / carbon composite material is machined into a workpiece with a diameter of 40 mm and a height of 10 mm, which is loaded into a graphite mold in an SPS furnace and pre-pressed with a force of 5KN to keep the surface of the sample flat.
[0040] (3) Using SPS furnace, vacuumize to 10 -2 After Pa, the carbon / carbon composite material is rapidly heated to a temperature of 1700°C, then slowly pressurized to a pressure of 31MPa, the temperature rise rate is controlled to be 140°C / min, and the pressurization rate is 0.5MPa / min;
[0041] (4) Insulation and pressure holding for 25 minutes, cooling and pressure ...
Embodiment 2
[0043] (1) Set the initial density to 0.15g / cm 3 The carbon fiber full mesh tire felt is densified to 1.32g / cm by CVI 3 , control the pyrolytic carbon microstructure of the substrate to rough layer structure pyrolytic carbon; CVI process parameters are: temperature: 1190 °C; pressure: 12kPa; propylene flow rate: 5.0L / min; nitrogen flow rate: 8L / min; time: 80h.
[0044](2) The carbon / carbon composite material is machined into a workpiece with a diameter of 40 mm and a height of 10 mm, which is loaded into a graphite mold in an SPS furnace and pre-pressed with a force of 5KN to keep the surface of the sample flat.
[0045] (3) Using SPS furnace, vacuumize to 10 -2 After Pa, the carbon / carbon composite material is rapidly heated to a temperature of 2000°C, then slowly pressurized to a pressure of 35MPa, and the temperature rise rate is controlled to be 120K / min, and the pressurization rate is 0.6MPa / min;
[0046] (4) Insulation and pressure holding for 30 minutes, cooling and p...
Embodiment 3
[0048] (1) Set the initial density to 0.2g / cm 3 The carbon fiber full mesh felt is densified to 1.15g / cm by CVI 3 , control the pyrolytic carbon microstructure of the substrate to rough layer structure pyrolytic carbon; CVI process parameters are: temperature: 1200 °C; pressure: 12kPa; methane flow rate: 7.0L / min; nitrogen flow rate: 11L / min; time: 70h.
[0049] (2) The carbon / carbon composite material is machined into a workpiece with a diameter of 40 mm and a height of 10 mm, which is loaded into a graphite mold in an SPS furnace and pre-pressed with a force of 5KN to keep the surface of the sample flat.
[0050] (3) Using SPS furnace, vacuumize to 10 -2 After Pa, the carbon / carbon composite material is rapidly heated to a temperature of 2100°C, then slowly pressurized to a pressure of 38MPa, and the temperature increase rate is controlled to be 180K / min, and the pressurization rate is 0.8MPa / min;
[0051] (4) Insulation and pressure holding for 15 minutes, cooling and pre...
PUM
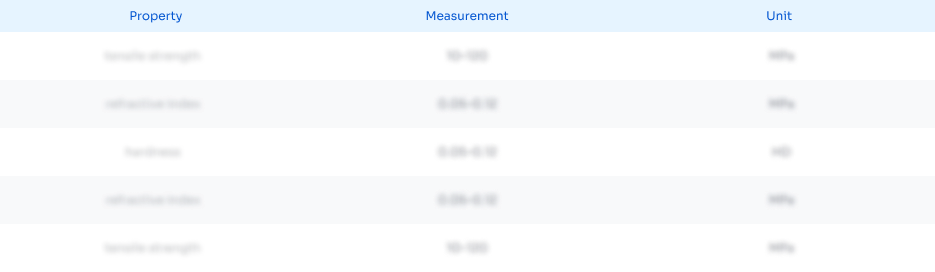
Abstract
Description
Claims
Application Information

- Generate Ideas
- Intellectual Property
- Life Sciences
- Materials
- Tech Scout
- Unparalleled Data Quality
- Higher Quality Content
- 60% Fewer Hallucinations
Browse by: Latest US Patents, China's latest patents, Technical Efficacy Thesaurus, Application Domain, Technology Topic, Popular Technical Reports.
© 2025 PatSnap. All rights reserved.Legal|Privacy policy|Modern Slavery Act Transparency Statement|Sitemap|About US| Contact US: help@patsnap.com