A kind of production technology of ladle drainage agent
A production process and technology of drainage agent, applied in the field of production technology of ladle drainage agent, can solve the problems of product stability impact, low heat utilization efficiency, increased labor cost, etc., to reduce the number of operators, high heat utilization efficiency, lower The effect of labor cost
- Summary
- Abstract
- Description
- Claims
- Application Information
AI Technical Summary
Problems solved by technology
Method used
Image
Examples
Embodiment 1
[0039] The ladle drainage sand in a steel factory has a product formula that includes 60-70 parts of chrome ore, 5-15 parts of alumina balls, 20-30 parts of desert sand and 1-5 parts of a performance modifier. The performance modifier is A mixture of flake graphite, super carbon black and semi-reinforcing carbon black in any proportion; among them, Cr in chrome ore 2 o 3 The content of SiO is ≥45%, the particle size is 0.2~0.9mm, and the 80 mesh is ≤3%, the 20 mesh is ≤2%, the water content is ≤0.5%, by weight percentage; SiO in desert sand 2 The content of ≥94%, the particle size is 0.5~1.2mm.
[0040] Adopt the production technology of ladle draining agent of the present invention to produce above-mentioned ladle draining agent, can carry out as follows:
[0041] A. According to the particle size requirements of the raw materials in the product formula, sieve the chrome ore and desert sand to the corresponding particle size, measure and sieve the components of each raw mat...
Embodiment 2
[0043] The ladle drainage sand in a steel factory, the product formula is chrome sand 60~76%, of which Cr in chrome sand 2 o 3 The mass percentage content of ≥45%; sea sand 10~20%, alumina ball 4~9%, desert sand 4~9%, potassium feldspar 3~5%, carbon black 0.3~0.8%, flake graphite 0.3~ 1.0%.
[0044] The production process of the ladle draining agent of the present invention is adopted to produce the above-mentioned ladle draining agent, and its production steps are the same as in Example 1, except that in step B, during the drying process, the rotating speed of the drum kang is controlled at 450 rpm, and the The wind temperature is controlled at 200°C; in step G, carbon black and flake graphite are fed from a separate silo into a closed stirring tank, and the stirring time is controlled at 20 minutes to obtain a finished product.
Embodiment 3
[0046] The ladle drainage agent in a steel factory is made of the following raw materials: its mass percentage distribution is as follows: chrome sand 50-80%, white quartz sand 10-30%, fused magnesia 8-20%, and the particle size of each raw material is controlled within the required range Inside.
[0047] The production process of the ladle draining agent of the present invention is adopted to produce the above-mentioned ladle draining agent, and its production steps are the same as in Example 1, the difference is: step B, in the drying process, the rotating speed of the drum kang is controlled at 300 rpm, and the The air temperature is controlled at 150°C; in step G, the fused magnesia is discharged from a separate silo into a closed stirring tank, and the stirring time is controlled at 30 minutes to obtain a finished product.
PUM
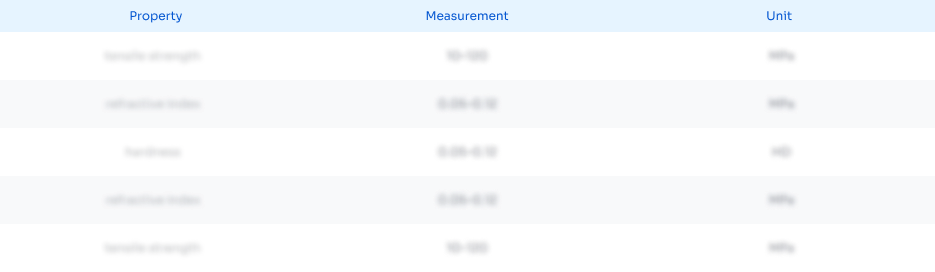
Abstract
Description
Claims
Application Information

- Generate Ideas
- Intellectual Property
- Life Sciences
- Materials
- Tech Scout
- Unparalleled Data Quality
- Higher Quality Content
- 60% Fewer Hallucinations
Browse by: Latest US Patents, China's latest patents, Technical Efficacy Thesaurus, Application Domain, Technology Topic, Popular Technical Reports.
© 2025 PatSnap. All rights reserved.Legal|Privacy policy|Modern Slavery Act Transparency Statement|Sitemap|About US| Contact US: help@patsnap.com