Processing method of interval transfer printing knitted bubble fabric
A transfer printing and processing method technology, applied in knitting, weft knitting, fabric surface trimming, etc., to achieve the effect of fast diffusion, bright colors, and high dye exhaustion rate
- Summary
- Abstract
- Description
- Claims
- Application Information
AI Technical Summary
Problems solved by technology
Method used
Image
Examples
specific Embodiment 1
[0049] A processing method for interval transfer printing knitted bubble fabric, comprising the following steps:
[0050] Gray cloth→pre-setting→pretreatment→dyeing→dehydration→cutting→setting→heat transfer printing→inspection→packaging;
[0051]In the gray cloth, the raw materials are: 150D / 72F cationic modified DTY polyester yarn, 75D / 72F glossy fine denier polyester filament and 40D spandex yarn; the weaving method is: 8-way 150D / 72F cationic modified DTY polyester yarn +8 channels of 75D / 72F glossy fine denier polyester filament and 40D spandex weaving at intervals; weaving equipment: 28-pin weft knitting circular machine weaving, product specification: gram weight 120G / M 2 , door width 150CM.
[0052] In the presetting step, the temperature is: 165°C, the vehicle speed is: 30m / min, and the grammage is: 120G / M 2 , door width: 150CM.
[0053] In the pretreatment step, the process prescription is: degreaser: 0.8g / L; process condition: 90°C*10min.
[0054] In the dyeing s...
specific Embodiment 2
[0076] A processing method for interval transfer printing knitted bubble fabric, comprising the following steps:
[0077] Gray cloth→pre-setting→pretreatment→dyeing→dehydration→cutting→setting→heat transfer printing→inspection→packaging;
[0078] In the gray cloth, the raw materials are: 150D / 72F cationic modified DTY polyester yarn, 75D / 72F glossy fine denier polyester filament and 40D spandex yarn; the weaving method is: 8-way 150D / 72F cationic modified DTY polyester yarn +8 channels of 75D / 72F bright fine denier polyester filament and 40D spandex weaving at intervals; weaving equipment: 28-pin weft knitting circular machine weaving, product specification: gram weight 130G / M 2 , door width 152CM.
[0079] In the presetting step, the temperature is: 170°C, the vehicle speed is: 50m / min, and the grammage is: 130G / M 2 , door width: 152CM.
[0080] In the pretreatment step, the process prescription is: degreaser: 1.0g / L; process condition: 90°C*20min.
[0081] In the dyeing ...
specific Embodiment 3
[0103] A processing method for interval transfer printing knitted bubble fabric, comprising the following steps:
[0104] Gray cloth→pre-setting→pretreatment→dyeing→dehydration→cutting→setting→heat transfer printing→inspection→packaging;
[0105] In the gray cloth, the raw materials are: 150D / 72F cationic modified DTY polyester yarn, 75D / 72F glossy fine denier polyester filament and 40D spandex yarn; the weaving method is: 8-way 150D / 72F cationic modified DTY polyester yarn +8 channels of 75D / 72F glossy fine denier polyester filament and 40D spandex weaving at intervals; weaving equipment: 28-needle weft knitting circular machine weaving, product specification: gram weight 124G / M 2 , door width 151CM.
[0106] In the presetting step, the temperature is: 162°C, the vehicle speed is: 40m / min, and the grammage is: 126G / M 2 , door width: 151CM.
[0107] In the pretreatment step, the process prescription is: degreaser: 0.9g / L; process condition: 90°C*14min.
[0108] In the dyei...
PUM
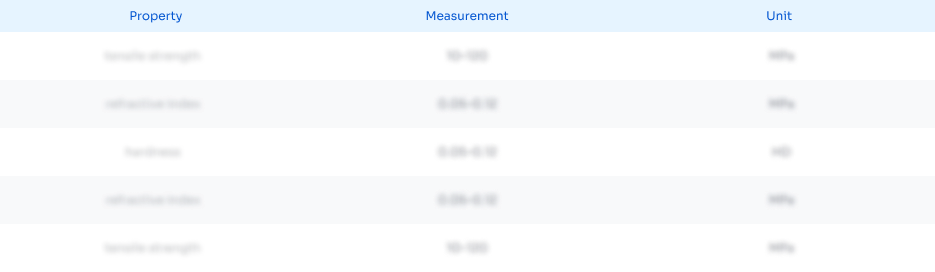
Abstract
Description
Claims
Application Information

- Generate Ideas
- Intellectual Property
- Life Sciences
- Materials
- Tech Scout
- Unparalleled Data Quality
- Higher Quality Content
- 60% Fewer Hallucinations
Browse by: Latest US Patents, China's latest patents, Technical Efficacy Thesaurus, Application Domain, Technology Topic, Popular Technical Reports.
© 2025 PatSnap. All rights reserved.Legal|Privacy policy|Modern Slavery Act Transparency Statement|Sitemap|About US| Contact US: help@patsnap.com