Separated continuous roll forming process for processing continuous twin-beam light steel room-frame component
A roll forming and separation technology, applied in the direction of truss structure, joists, girders, etc., can solve the problems of difficult transportation and installation of components, difficult control of processing accuracy, etc., and achieve the effect of saving equipment cost and investment.
- Summary
- Abstract
- Description
- Claims
- Application Information
AI Technical Summary
Problems solved by technology
Method used
Image
Examples
Embodiment Construction
[0030] In order to further explain the technical means and effects of the present invention to achieve the predetermined purpose, the following is combined with the accompanying drawings and preferred embodiments, and the beam-column components of the continuous double-girder light steel roof truss proposed according to the present invention are separated and continuously rolled. The specific implementation, features and effects of the processing technology are as follows in detail.
[0031] see figure 1 Shown, it shows the scheme of a preferred embodiment of the present invention. In this example, the preprocessing step B and the continuous roll forming step D are run independently of each other, but in succession to each other, ie consecutively at the same site. Between the preprocessing step B and the continuous roll forming step D, a buffer space C is provided. The separation-type continuous roll forming process of the beam-column components of the continuous double-gird...
PUM
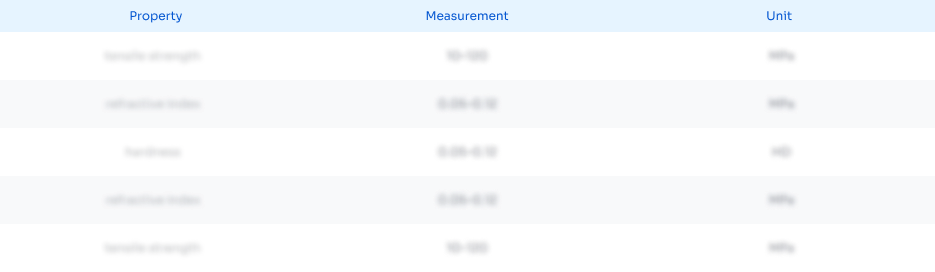
Abstract
Description
Claims
Application Information

- R&D
- Intellectual Property
- Life Sciences
- Materials
- Tech Scout
- Unparalleled Data Quality
- Higher Quality Content
- 60% Fewer Hallucinations
Browse by: Latest US Patents, China's latest patents, Technical Efficacy Thesaurus, Application Domain, Technology Topic, Popular Technical Reports.
© 2025 PatSnap. All rights reserved.Legal|Privacy policy|Modern Slavery Act Transparency Statement|Sitemap|About US| Contact US: help@patsnap.com