Investment casting pouring method of thin-wall aluminum alloy casting
An aluminum alloy casting and investment casting technology, which is applied in the pouring process field of investment casting of thin-walled aluminum alloy castings, can solve the problems of insufficient pouring corners, high scrap rate, and unguaranteed product quality, so as to reduce cooling speed and improve Fluidity, effect of eliminating pinholes and shrinkage defects
- Summary
- Abstract
- Description
- Claims
- Application Information
AI Technical Summary
Problems solved by technology
Method used
Examples
Embodiment
[0016] The casting material of the disc-shaped impeller is: ZL101.
[0017] Disc-shaped impeller investment casting mainly includes the following steps:
[0018] 1. Manufacture of formwork:
[0019] The manufacture of the formwork proceeds in the following steps:
[0020] Step 1. First, press the wax mold at a temperature of 50-56°C in the wax injection pipe. After the wax mold is taken out, immediately put it in a special shaping tool to cool it to prevent the wax mold from deforming;
[0021] Step 2, the wax pattern is assembled and welded;
[0022] Step 3: Carry out shell making (slurry, sand covering) and drying of the assembled and welded modules in an environment with a temperature of 24±2°C and a humidity of 40-70%;
[0023] Step 4: Dewaxing the module to obtain a mold shell. The module is dewaxed by steam, the dewaxing steam pressure is 0.55-0.75 MPa, and the time is 8-12 minutes.
[0024] 2. Mold shell roasting:
[0025] The baking temperature of the ...
PUM
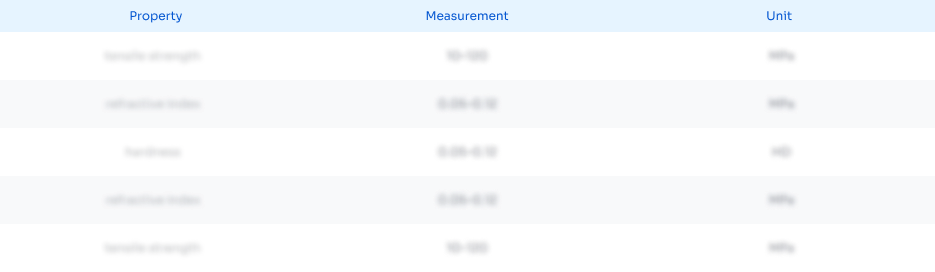
Abstract
Description
Claims
Application Information

- R&D
- Intellectual Property
- Life Sciences
- Materials
- Tech Scout
- Unparalleled Data Quality
- Higher Quality Content
- 60% Fewer Hallucinations
Browse by: Latest US Patents, China's latest patents, Technical Efficacy Thesaurus, Application Domain, Technology Topic, Popular Technical Reports.
© 2025 PatSnap. All rights reserved.Legal|Privacy policy|Modern Slavery Act Transparency Statement|Sitemap|About US| Contact US: help@patsnap.com