Preparation method of special inorganic anti-veining additive for casting
An additive and veining technology, used in casting molding equipment, metal processing equipment, casting molds, etc., can solve the problems of large weakening effect of sand mold strength, poor anti-veining effect, and small inhibition effect, so as to prevent casting veining. Grain defects, good anti-veining effect, anti-cracking effect
- Summary
- Abstract
- Description
- Claims
- Application Information
AI Technical Summary
Problems solved by technology
Method used
Examples
Embodiment 1
[0019] Embodiment one: a kind of preparation method of special inorganic anti-veining additive for casting, the method comprises the following steps:
[0020] a. Sieve iron oxide red and iron oxide black with a 70-mesh sieve respectively, discard the sieve, and keep the sieve residue for subsequent use;
[0021] b. Sieve the spodumene, kyanite, and hollow microspheres with a 30-mesh sieve respectively, discard the sieve, and keep the sieve residue for subsequent use;
[0022] c. Weigh 340kg of red iron oxide, 260kg of black iron oxide, 150kg of spodumene, 90kg of kyanite, and 80kg of hollow microspheres after sieving, weigh 50kg of lithium carbonate, and 30kg of potassium carbonate, and add special stirring and mixing equipment in turn, Then turn on the stirring for mixing, after the mixing is completed, the material is discharged.
Embodiment 2
[0023] Embodiment two: a kind of preparation method of special inorganic anti-veining additive for casting, the method comprises the following steps:
[0024] a. Sieve iron oxide red and iron oxide black with a 70-mesh sieve respectively, discard the sieve, and keep the sieve residue for subsequent use;
[0025] b. Sieve the spodumene, kyanite, and hollow microspheres with a 30-mesh sieve respectively, discard the sieve, and keep the sieve residue for subsequent use;
[0026] c. Weigh 300kg of red iron oxide, 280kg of black iron oxide, 180kg of spodumene, 80kg of kyanite, and 100kg of hollow microspheres after sieving, weigh 40kg of lithium carbonate, and 20kg of potassium carbonate, and then add special stirring and mixing equipment in turn. Then turn on the stirring for mixing, after the mixing is completed, the material is discharged.
Embodiment 3
[0027] Embodiment three: a kind of preparation method of casting special inorganic anti-veining additive, this method comprises the following steps:
[0028] a. Sieve iron oxide red and iron oxide black with a 70-mesh sieve respectively, discard the sieve, and keep the sieve residue for subsequent use;
[0029] b. Sieve the spodumene, kyanite, and hollow microspheres with a 30-mesh sieve respectively, discard the sieve, and keep the sieve residue for subsequent use;
[0030] c. Weigh 400kg of red iron oxide, 250kg of black iron oxide, 120kg of spodumene, 100kg of kyanite, 60kg of hollow microspheres after sieving, weigh 30kg of lithium carbonate, and 40kg of potassium carbonate, and add special stirring and mixing equipment in turn, Then turn on the stirring for mixing, after the mixing is completed, the material is discharged.
PUM
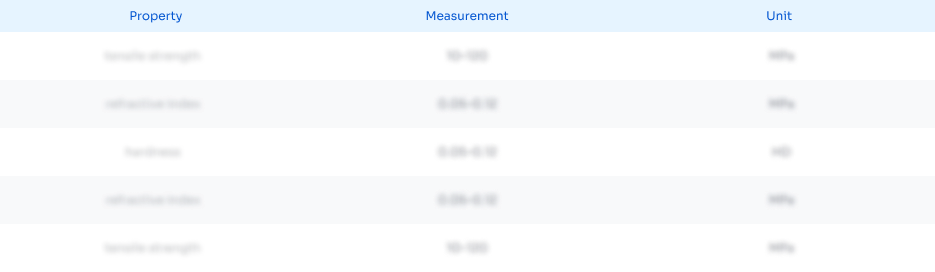
Abstract
Description
Claims
Application Information

- R&D
- Intellectual Property
- Life Sciences
- Materials
- Tech Scout
- Unparalleled Data Quality
- Higher Quality Content
- 60% Fewer Hallucinations
Browse by: Latest US Patents, China's latest patents, Technical Efficacy Thesaurus, Application Domain, Technology Topic, Popular Technical Reports.
© 2025 PatSnap. All rights reserved.Legal|Privacy policy|Modern Slavery Act Transparency Statement|Sitemap|About US| Contact US: help@patsnap.com