Preparation method of reinforced fiber for special paper
A technology for reinforcing fiber and special paper, applied in the direction of fiber type, fiber treatment, fiber raw material treatment, etc., to achieve the effect of solving serious shortage, improving dispersion, and overcoming paper sticking
- Summary
- Abstract
- Description
- Claims
- Application Information
AI Technical Summary
Problems solved by technology
Method used
Examples
preparation example Construction
[0024] The specific steps of the method for preparing the reinforcing fiber for special paper of the present invention will be described in detail below.
[0025] 1) In parts by mass, add 1 part of polyvinyl alcohol fiber and 50-100 parts of organic solvent into the reactor, stir well and add 0.2-1 part of 4-dimethylaminopyridine (high-efficiency acylation reaction catalyst) and 1 ~2 parts of triethylamine (acid-binding agent) shake well, place in ice-water bath, fill with N 2 To remove the air in the reactor, so that the resulting reaction system is in an oxygen-free environment; slowly drop into the reaction system an organic compound of an acylating agent mixed with 1.3-2.5 parts of an acylating agent and 6-12 parts of an organic solvent. Solution, the dropping time is controlled within 1~2h; then react in an ice-water bath and anaerobic environment for 2~4h, then raise the temperature to 20-40°C, and react for 12~48h to obtain a reaction solution containing the crude produ...
Embodiment 1
[0036] 1) According to the number of parts by mass, add 1 part of water-insoluble polyvinyl alcohol fiber and 50 parts of N-methylpyrrolidone into the reactor, stir well, add 0.5 part of 4-dimethylaminopyridine and 1 part of triethylamine and shake well , placed in an ice-water bath, filled with N 2 In order to remove the air in the reactor, the resulting reaction system is in an oxygen-free environment; slowly drop into the reaction system 2-bromo In the organic solution of isobutyryl bromide, the dropping time is controlled within 1 hour, then reacted in an ice-water bath and an oxygen-free environment for 3 hours, then heated up to 30°C, and reacted for 18 hours to obtain a reaction solution containing the crude product; The reaction solution was suction filtered, and then the obtained PVA fiber macromolecular initiator filter cake was washed alternately with ethanol and water to remove residual impurities on the fiber surface, and finally dried in a vacuum drying oven at 5...
Embodiment 2
[0040] 1) According to the number of parts by mass, add 1 part of water-soluble polyvinyl alcohol fiber and 80 parts of tetrahydrofuran into the reactor, stir well, add 0.8 part of 4-dimethylaminopyridine and 1 part of triethylamine and shake well, place In an ice water bath, filled with N 2 In order to remove the air in the reactor, the resulting reaction system is in an oxygen-free environment; slowly drop 2-bromoisobutyryl bromide formed by mixing 2.5 parts of 2-bromoisobutyryl bromide and 12 parts of tetrahydrofuran into the reaction system In the organic solution of bromine, the dropping time is controlled within 2 hours, then reacted in an ice-water bath and an oxygen-free environment for 4 hours, then heated up to 30°C, and reacted for 48 hours to obtain a reaction solution containing a crude product; pump the reaction solution containing a crude product filter, and then alternately wash the obtained PVA fiber macroinitiator filter cake with ethanol and water to remove ...
PUM
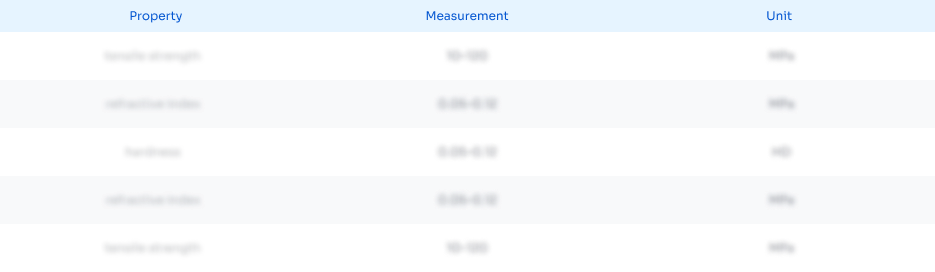
Abstract
Description
Claims
Application Information

- R&D Engineer
- R&D Manager
- IP Professional
- Industry Leading Data Capabilities
- Powerful AI technology
- Patent DNA Extraction
Browse by: Latest US Patents, China's latest patents, Technical Efficacy Thesaurus, Application Domain, Technology Topic, Popular Technical Reports.
© 2024 PatSnap. All rights reserved.Legal|Privacy policy|Modern Slavery Act Transparency Statement|Sitemap|About US| Contact US: help@patsnap.com