Manufacturing method of alloy steel for high and cold zone motor shaft
A manufacturing method and technology of alloy steel, applied in the direction of manufacturing tools, quenching agents, heat treatment equipment, etc., can solve the problems of complicated process, unable to meet the production cost of 42CrMo, unsuitable for industrialized large-scale production, etc., achieve simple process and reduce production cost Effect
- Summary
- Abstract
- Description
- Claims
- Application Information
AI Technical Summary
Problems solved by technology
Method used
Image
Examples
Embodiment 1)
[0019] This embodiment is a method for manufacturing alloy steel for motor shafts in alpine regions with a specification of Φ210mm*2955mm, including:
[0020] ① Smelt and forge 42CrMo material roll blanks according to the conventional process.
[0021] ②After the rough machining of the roll billet, heat it to 800°C for 25 hours for tempering and quenching treatment, and then cool it with polyvinylpyrrolidone (PVP) aqueous solution.
[0022] ③Heat the tempered and quenched roll blank to 620°C for tempering treatment, keep it warm for 20 hours and then air cool it.
[0023] Test the impact energy at -20°C near the surface and 1 / 2 radius of the motor shaft, and the results are shown in Table 1.
Embodiment 2~ Embodiment 4)
[0025] Each embodiment is basically the same as Embodiment 1, and the differences are shown in Table 1.
[0026] Table 1
[0027] Example 1 Example 2 Example 3 Example 4 Quenching temperature 800℃ 810℃ 800℃ 790℃ Quenching time 25h 20h 25h 30h Motor Shaft Specifications Φ210mm*2955mm Φ210mm*2955mm Φ288mm*2714.5mm Φ288mm*2714.5mm Near surface impact energy at -20°C 50J 44J 46J 45J Impact energy at -20°C at 1 / 2 radius 47J 40J 43J 41J
PUM
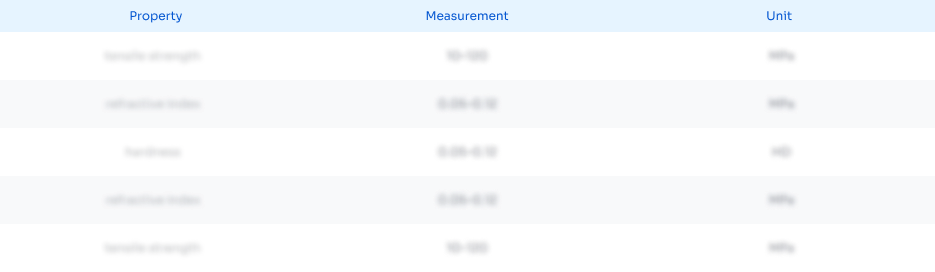
Abstract
Description
Claims
Application Information

- R&D
- Intellectual Property
- Life Sciences
- Materials
- Tech Scout
- Unparalleled Data Quality
- Higher Quality Content
- 60% Fewer Hallucinations
Browse by: Latest US Patents, China's latest patents, Technical Efficacy Thesaurus, Application Domain, Technology Topic, Popular Technical Reports.
© 2025 PatSnap. All rights reserved.Legal|Privacy policy|Modern Slavery Act Transparency Statement|Sitemap|About US| Contact US: help@patsnap.com