Prepration method of nanometer material capable of improving fire resistance of waterborne polyurethane coating and adhesive
A water-based polyurethane and nanomaterial technology, applied in polyurea/polyurethane coatings, polyurea/polyurethane adhesives, adhesives, etc., can solve problems such as environmental hazards of heavy metals and tin
- Summary
- Abstract
- Description
- Claims
- Application Information
AI Technical Summary
Problems solved by technology
Method used
Examples
example 1
[0047] (1) Add 3.0g of carbon nanotubes and 250g of concentrated nitric acid into a 500ml three-neck flask, stir at room temperature for 24 hours, then wash with deionized water until the pH of the solution is neutral, dry at 100°C overnight, grind for later use to obtain pretreated carbon nanotubes tube; weigh 1.0 g of pretreated carbon nanotubes, add 60 g of triethylene glycol, ultrasonicate for 5 min, and then add Fe(acac) 3 1.5g, continue to sonicate for 10min, pass in nitrogen, heat until the solution boils, reflux for 0.5h, cool to room temperature, wash with ethanol until colorless, and dry at 80°C overnight to obtain Fe 3 o 4 / CNT carrier; weigh Pd(acac) 2 0.0446g, 0.1135g of 1,2-hexadecane glycol, 20g of dioctyl ether and 0.12g of dipotassium edetate, blowing nitrogen gas, heating to 100°C, adding 0.5g Fe 3 o 4 / CNT carrier, continue to heat to boiling, reflux for 0.5h, cool to room temperature, close the protective gas, filter with suction, wash with absolute etha...
example 2
[0053] (1) Add 3.0g of carbon nanotubes to a 500ml three-neck flask, add 250g of concentrated nitric acid, stir at room temperature for 24 hours, then wash with deionized water until the pH of the solution is neutral, dry at 100°C overnight, and grind to obtain pretreated carbon Nanotubes: Weigh 1.0 g of pretreated carbon nanotubes, add 60 g of triethylene glycol, ultrasonicate for 5 minutes, and then add Fe(acac) 3 1.5g, continue to sonicate for 10min, pass in nitrogen, heat until the solution boils, reflux for 0.5h, cool to room temperature, wash with ethanol until colorless, and dry at 80°C overnight to obtain Fe 3 o 4 / CNT carrier; weigh Pd(acac) 2 0.0446g, 0.1135g of 1,2-hexadecanediol, 20g of dioctyl ether and 0.78g of 3-carboxypyridazine, blow nitrogen, heat to 100°C, add 0.5g Fe 3 o 4 / CNT carrier, continue to heat to boiling, reflux for 0.5h, cool to room temperature, close the protective gas, filter with suction, wash with absolute ethanol until colorless, and dr...
example 3
[0060] (1) Add 3.0g of carbon nanotubes to a 500ml three-neck flask, add 250g of concentrated nitric acid, stir at room temperature for 24 hours, then wash with deionized water until the pH of the solution is neutral, dry at 100°C overnight, and grind to obtain pretreated carbon Nanotubes: Weigh 1.0 g of pretreated carbon nanotubes, add 60 g of triethylene glycol, ultrasonicate for 5 minutes, and then add Fe(acac) 3 1.5g, continue to sonicate for 10min, pass in nitrogen, heat until the solution boils, reflux for 0.5h, cool to room temperature, wash with ethanol until colorless, and dry at 80°C overnight to obtain Fe 3 o 4 / CNT carrier; weigh Pd(acac) 2 0.0446g, 0.1135g of 1,2-hexadecane diol, 20g of dioctyl ether and 0.34g of potassium 2-carboxy-5-nitrobenzenesulfonate, blow nitrogen, heat to 100°C, add 0.5g Fe 3 o 4 / CNT carrier, continue to heat to boiling, reflux for 0.5h, cool to room temperature, close the protective gas, filter with suction, wash with absolute ethano...
PUM
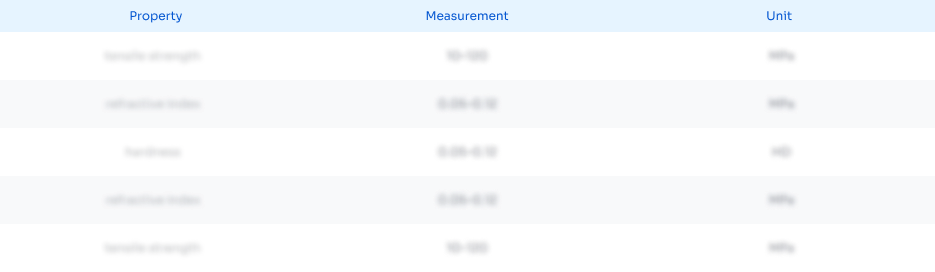
Abstract
Description
Claims
Application Information

- R&D
- Intellectual Property
- Life Sciences
- Materials
- Tech Scout
- Unparalleled Data Quality
- Higher Quality Content
- 60% Fewer Hallucinations
Browse by: Latest US Patents, China's latest patents, Technical Efficacy Thesaurus, Application Domain, Technology Topic, Popular Technical Reports.
© 2025 PatSnap. All rights reserved.Legal|Privacy policy|Modern Slavery Act Transparency Statement|Sitemap|About US| Contact US: help@patsnap.com