Preparation method of metallocene catalyst
A technology of metallocene catalysts and metallocene compounds, which is applied in the field of preparation of metallocene catalysts and can solve the problems of reducing the aging resistance of polymers
- Summary
- Abstract
- Description
- Claims
- Application Information
AI Technical Summary
Problems solved by technology
Method used
Image
Examples
Embodiment 1
[0034] In 500 mL of tetrahydrofuran, add 4 g of triisobutylaluminum and 0.5 g of nickel acetylacetonate to react at room temperature for 2 hours, then add 5 g of Davison955 silica (commercially available) from Grace Company to continue the reaction at room temperature for 4 hours, and remove the solvent Store in nitrogen gas for later use.
[0035]20 g of 10% by mass percentage of methylaluminoxane toluene solution and 0.15 g of bis(pentamethylcyclopentadienyl) zirconium dichloride were stirred at 50°C for 2 hours to obtain the catalyst mother liquor,
[0036] Then silica gel was added into the mother liquor, the reaction was continued at -10°C for 4 hours, and the solid powder catalyst was obtained after removing the solvent.
Embodiment 2
[0043] In 500mL of tetrahydrofuran, add 7g of triisobutylaluminum and 1g of cobalt acetylacetonate to react for 1 hour at -10°C, then add 15g of Davison955 silicon dioxide from Grace Company and react at room temperature for 6 hours. After removing the solvent, seal the obtained silica gel with nitrogen until use.
[0044] 10 g of 10% by mass percentage of methylaluminoxane toluene solution and 0.05 g of bis(tert-butylcyclopentadienyl) zirconium dichloride were stirred at 70° C. for 4 hours to obtain the catalyst mother liquor,
[0045] Then silica gel was added to the mother liquor, the reaction was continued at -10°C for 6 hours, and the solid powder catalyst was obtained after removing the solvent.
Embodiment 3
[0047] In 500mL of tetrahydrofuran, add 1g of triisobutylaluminum and 0.25g of nickel acetylacetonate to react at 50°C for 3 hours, then add 23g of Davison955 silicon dioxide from Grace Company at 50°C for 4 hours, remove the solvent and seal the obtained silica gel with nitrogen stand-by.
[0048] 100 g of 10% by mass percentage of methylaluminoxane toluene solution and 8 g of bis(n-butylcyclopentadienyl) zirconium dichloride were stirred at 50° C. for 2 hours to obtain the catalyst mother liquor,
[0049] Then silica gel was added into the mother liquor, the reaction was continued at -10°C for 4 hours, and the solid powder catalyst was obtained after removing the solvent.
PUM
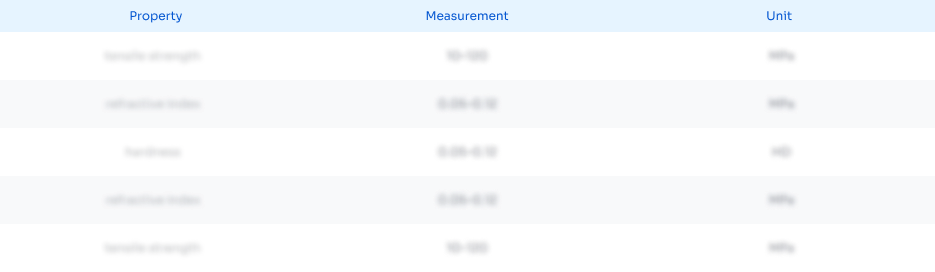
Abstract
Description
Claims
Application Information

- R&D
- Intellectual Property
- Life Sciences
- Materials
- Tech Scout
- Unparalleled Data Quality
- Higher Quality Content
- 60% Fewer Hallucinations
Browse by: Latest US Patents, China's latest patents, Technical Efficacy Thesaurus, Application Domain, Technology Topic, Popular Technical Reports.
© 2025 PatSnap. All rights reserved.Legal|Privacy policy|Modern Slavery Act Transparency Statement|Sitemap|About US| Contact US: help@patsnap.com