Purification method of polyoxymethylene dimethyl ether
A technology of dimethyl ether and purification method, applied in chemical instruments and methods, preparation of organic compounds, organic chemistry, etc., to reduce the possibility of clogging and improve efficiency
- Summary
- Abstract
- Description
- Claims
- Application Information
AI Technical Summary
Problems solved by technology
Method used
Image
Examples
Embodiment 1
[0033] Using paraformaldehyde and methylal as raw materials, polyoxymethylene dimethyl ether is synthesized by trifluorosulfonic acid catalysis. After the reaction, the pH value of the reaction mixture is adjusted to PH=7.5. The composition of the reaction mixture to be separated was detected as follows: Methanol, 3.9%; Methylal, 40.56%; Paraformaldehyde, 8.5%; n=2, 23.02%; n=3, 12.30%; n=4, 6.31%; n =5, 3.14%; n>5, margin. Under the operating condition of the reflux ratio of 0.5, the distillation tower top temperature is 41°C to remove the first fraction; the first rectification tower is operating at the operating pressure of 0.05Mpa and the reflux ratio of 3 conditions, and the top temperature of 69~71°C is separated. second fraction. The bottom liquid of the second column was cooled to room temperature, and the solid paraformaldehyde was removed through centrifugation; the pressure of the second rectification column was 0.025Mpa, and the reflux ratio was 8, and the third f...
Embodiment 2
[0035] The sulfuric acid catalyzed reaction mixture of methylal and paraformaldehyde consisted of: methanol, 3.3%; methylal, 33.19%; paraformaldehyde, 10.5%; n=2, 25.15%; n=3, 13.44%; n =4, 6.88%; n=5, 3.43%; n>5, margin. After the reaction, the pH value of the reaction mixture was adjusted to pH=7. Under the operating condition that the reflux ratio is 1, the temperature at the top of the distillation column is 43°C to remove the first fraction; the first fraction is separated at the operating pressure of 0.1Mpa and the reflux ratio is 5, and the second fraction with a top temperature of 103°C is separated. fraction. After removing the second fraction, the liquid in the second column was cooled to -10°C, and the solid paraformaldehyde in it was removed by low-temperature suction filtration; the pressure of the second rectification column was 0.005Mpa, and the reflux ratio was 6, and the top of the column was collected The third fraction at a temperature of 70 °C. The analy...
Embodiment 3
[0041] The sulfuric acid catalyzed reaction mixture of methylal and paraformaldehyde consisted of: methanol, 3.3%; methylal, 33.19%; paraformaldehyde, 10.5%; n=2, 25.15%; n=3, 13.44%; n =4, 6.88%; n=5, 3.43%; n>5, margin. After the reaction, the pH value of the reaction mixture was adjusted to pH=6.5. Under the operating condition that the reflux ratio is 3, the temperature at the top of the distillation column is 45°C to remove the first fraction; the first fraction is separated at the operating pressure of 0.06Mpa and the reflux ratio is 1, and the second fraction with a top temperature of 85°C is separated. fraction. After removing the second fraction, the liquid in the second tower was cooled to -20°C, and filtered under low-temperature and reduced pressure to remove the solid paraformaldehyde; the second rectification tower was under the condition of a pressure of 0.05Mpa and a reflux ratio of 4. A third fraction was collected with an overhead temperature of 170°C. The...
PUM
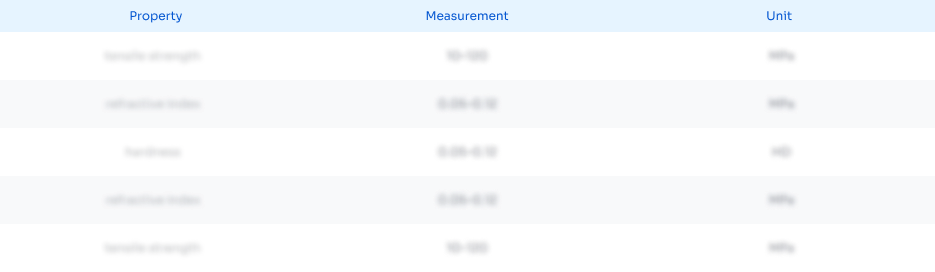
Abstract
Description
Claims
Application Information

- R&D Engineer
- R&D Manager
- IP Professional
- Industry Leading Data Capabilities
- Powerful AI technology
- Patent DNA Extraction
Browse by: Latest US Patents, China's latest patents, Technical Efficacy Thesaurus, Application Domain, Technology Topic, Popular Technical Reports.
© 2024 PatSnap. All rights reserved.Legal|Privacy policy|Modern Slavery Act Transparency Statement|Sitemap|About US| Contact US: help@patsnap.com