Method and equipment for processing exhaust gases of volatile organic compounds
An organic compound and volatile technology, applied in the field of volatile organic compound waste gas treatment, can solve the problems of difficult treatment, expensive equipment, catalyst, limited treatment capacity, etc., and achieve flexible equipment, good economic and environmental benefits, and flexible assembly Effect
- Summary
- Abstract
- Description
- Claims
- Application Information
AI Technical Summary
Problems solved by technology
Method used
Image
Examples
Embodiment 1
[0050] Example 1-VOCs exhaust gas treatment from a contaminated soil gas phase extraction:
[0051] In this example, the VOCs exhaust gas 1 (500NM 3 / hr), its total concentration after testing is as high as 25100ppm. The VOCs exhaust gas 1 enters the gas compressor C2 through the blower C1. The outlet pressure of C2 is 1MPa and the temperature is 50°C; the gas compressor outlet stream 3 is cooled to 5°C through the precooler F1 and then enters the direct contact deep cooling tower T1. The T1 pressure of the direct contact deep cooling tower is 1MPa, and the liquid phase inlet stream 9 of the direct contact deep cooling tower is the starting refrigerant (refrigerant flow) at -45°C. At the bottom, the bottom of the tower is generated after the starting refrigerant contacts with VOCs Part of the liquid organic matter enters the waste liquid collection tank V1, and a part of the waste liquid is reserved to enter the cryocooler F2 and is cooled to -45°C as the starting refrigerant. T...
Embodiment 2
[0055] Example 2-Treatment of VOCs discharged from a refinery:
[0056] In this example, the VOCs exhaust gas 1 (1000NM 3 / hr), its total concentration after detection is as high as 15100ppm. The VOCs exhaust gas 1 enters the gas compressor C2 through the blower C1. The outlet pressure of C2 is 2MPa and the temperature is 75°C; the gas compressor outlet stream 3 is cooled to 0°C through the precooler F1 and then enters the direct contact deep cooling tower T1. The T1 pressure of the direct contact deep cooling tower is 2MPa, and the liquid phase inlet stream 9 of the direct contact deep cooling tower uses the starting refrigerant (refrigerant flow) at -85℃. At the bottom, the bottom of the tower is produced after the starting refrigerant contacts with VOCs. A part of the liquid organic matter enters the waste liquid collection tank V1, and a part of the waste liquid is reserved to enter the cryocooler F2 and is cooled to -85°C as the starting refrigerant. The temperature of the ...
Embodiment 3
[0060] Example 3-Treatment of VOCs discharged by a printing company:
[0061] In this example, a printing company’s VOCs exhaust gas 1 (1000NM 3 / hr), after testing the total concentration is as high as 26600ppm, the VOCs exhaust gas 1 enters the gas compressor C2 through the blower C1, the outlet pressure of C2 is 0.5MPa, and the temperature is 30℃; the gas compressor outlet stream 3 is cooled to by the precooler F1 After 22.5℃, enter the direct contact deep cooling tower T1. The pressure of the direct contact deep cooling tower T1 is 0.5MPa. The liquid phase inlet stream 9 of the direct contact deep cooling tower is the starting refrigerant (refrigerant flow) at -20℃. At the bottom, a part of the liquid phase organics at the bottom of the tower produced after the starting refrigerant contacts with VOCs enters the waste liquid collection tank V1, and a part of the waste liquid is reserved to enter the cryocooler F2 and be cooled to -20°C as the starting refrigerant. The temperat...
PUM
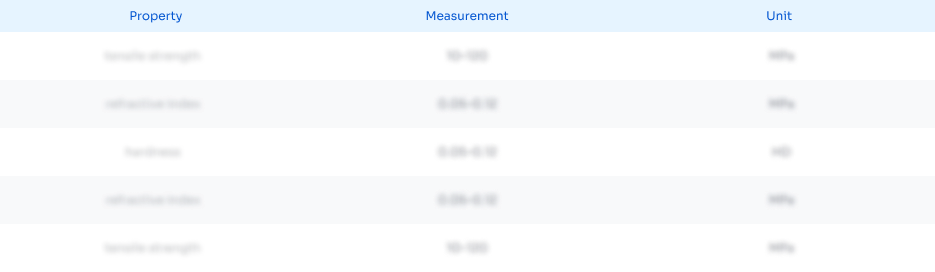
Abstract
Description
Claims
Application Information

- R&D Engineer
- R&D Manager
- IP Professional
- Industry Leading Data Capabilities
- Powerful AI technology
- Patent DNA Extraction
Browse by: Latest US Patents, China's latest patents, Technical Efficacy Thesaurus, Application Domain, Technology Topic, Popular Technical Reports.
© 2024 PatSnap. All rights reserved.Legal|Privacy policy|Modern Slavery Act Transparency Statement|Sitemap|About US| Contact US: help@patsnap.com