Measurement system and measurement method for stress waves of Hopkinson bars by using flexoelectric effect
A Hopkinson rod, flexoelectric effect technology, applied in force/torque/work measuring instruments, measuring devices, instruments, etc. Accuracy, Effects of High Stress Waveform Measurement Accuracy
- Summary
- Abstract
- Description
- Claims
- Application Information
AI Technical Summary
Problems solved by technology
Method used
Image
Examples
Embodiment Construction
[0031] The present invention will be described in further detail below in conjunction with the accompanying drawings and specific embodiments.
[0032] As shown in the accompanying drawings, the Hopkinson bar stress wave measurement system using the flexoelectric effect of the present invention includes a bullet 1, a laser velocimeter 2, an input rod 3, an output rod 6, an absorption rod 8 and a damper 9, respectively attached The first strain gradient sensor 4 and the second strain gradient sensor 7 on the input rod 3 and the output rod 6, the velocity measuring circuit 10 optically connected with the laser velocimeter 2, and the first strain gradient sensor 4 and the second strain gradient sensor 7 Two-way charge amplifier 11 electrically connected, wherein the output terminal of the speed measuring circuit 10 and the two-way charge amplifier 11 is electrically connected with the signal processing, display, and storage module 12; when measuring the stress wave, the test piece...
PUM
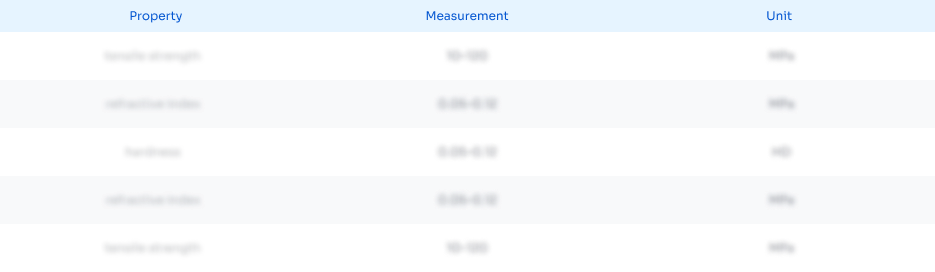
Abstract
Description
Claims
Application Information

- R&D Engineer
- R&D Manager
- IP Professional
- Industry Leading Data Capabilities
- Powerful AI technology
- Patent DNA Extraction
Browse by: Latest US Patents, China's latest patents, Technical Efficacy Thesaurus, Application Domain, Technology Topic, Popular Technical Reports.
© 2024 PatSnap. All rights reserved.Legal|Privacy policy|Modern Slavery Act Transparency Statement|Sitemap|About US| Contact US: help@patsnap.com