Extrusion processing method for external star wheel
A technology of extrusion processing and outer star wheel, which is applied in the field of metal processing, can solve the problems of difficult control of precision size, poor distribution of metal flow lines, low material utilization rate, etc., and achieve high anti-fatigue and breaking capacity, good compression internal stress , The effect of reducing material consumption
- Summary
- Abstract
- Description
- Claims
- Application Information
AI Technical Summary
Problems solved by technology
Method used
Image
Examples
Embodiment Construction
[0026] The processing steps of the invention are: blanking-heating-upsetting-warm extrusion-annealing-shot blasting-phosphating-saponification-cold extrusion-inspection.
[0027] Cutting according to the size of the part;
[0028] Start the intermediate frequency heating furnace; adjust the parameters of the intermediate frequency furnace: power (15-80KW), DC voltage (380-500V), DC current (100-200A);
[0029] Put 10 pieces of billets into the furnace first, heat for 80-150 seconds, push out the billets with the pusher cylinder at a frequency of 5-10 seconds per piece, and add another piece of billets to the furnace every time one is pushed out.
[0030] Upsetting the heated billet to the specified size.
[0031] Using CNC precision forging presses and special molds, the upsetting billets are back-extruded into part-sized billets with a pressure of 300T. Specific parameters such as the speed, frequency, force level, time and other specific parameters of the CNC precision for...
PUM
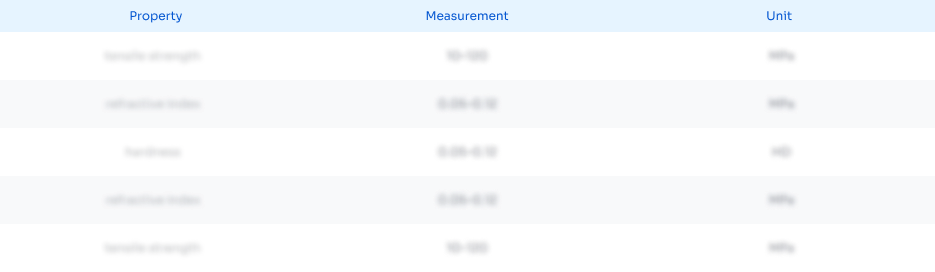
Abstract
Description
Claims
Application Information

- R&D
- Intellectual Property
- Life Sciences
- Materials
- Tech Scout
- Unparalleled Data Quality
- Higher Quality Content
- 60% Fewer Hallucinations
Browse by: Latest US Patents, China's latest patents, Technical Efficacy Thesaurus, Application Domain, Technology Topic, Popular Technical Reports.
© 2025 PatSnap. All rights reserved.Legal|Privacy policy|Modern Slavery Act Transparency Statement|Sitemap|About US| Contact US: help@patsnap.com