Technology for producing hollow slabs by recovering waste plastics
A technology of waste plastics and empty boards, which is applied to other household appliances, flat products, household appliances, etc., can solve the problems of not being able to use large areas, high cost of hollow boards, and easy aging, so as to improve the profit rate of enterprises and reduce production costs , Environmentally friendly effect
- Summary
- Abstract
- Description
- Claims
- Application Information
AI Technical Summary
Problems solved by technology
Method used
Image
Examples
Embodiment 1
[0016] 1. Pretreatment of recycled waste plastics: the recycled thermoplastic polypropylene waste plastics are crushed, cleaned, dried, added to a granulator to extrude and granulated, and recycled masterbatch is obtained;
[0017] 2. Weigh according to the following parts by weight: 40 parts of recycled masterbatch, 20 parts of new polypropylene masterbatch, 1 part of toughening agent, 1 part of antistatic agent, and 0.1 part of modifier;
[0018] 3. Add 40 parts of recycled masterbatch and 20 parts of new polypropylene masterbatch to the high-speed mixer for blending, and the speed of the high-speed mixer is 450-500r / min;
[0019] 4. Continue to add other additives into the high-speed mixer for blending, and the speed of the high-speed mixer is 800-1000r / min;
[0020] 5. Put the mixture obtained by blending into the screw extruder. The temperature of the melting and plasticizing section of the extruder is 150-170 degrees, the temperature of the equilibrium section is 170-190...
Embodiment 2
[0025] Weigh according to the following parts by weight: 60 parts of recycled masterbatch, 30 parts of new polypropylene masterbatch, 2 parts of toughening agent, 3 parts of antistatic agent, 3 parts of modifier; 2.
Embodiment 3
[0027] Weigh according to the following parts by weight: 50 parts of recycled masterbatch, 25 parts of new polypropylene masterbatch, 1.5 parts of toughening agent, 2 parts of antistatic agent, and 2 parts of modifier; other steps are the same as in Example 1 to obtain the sample 3.
PUM
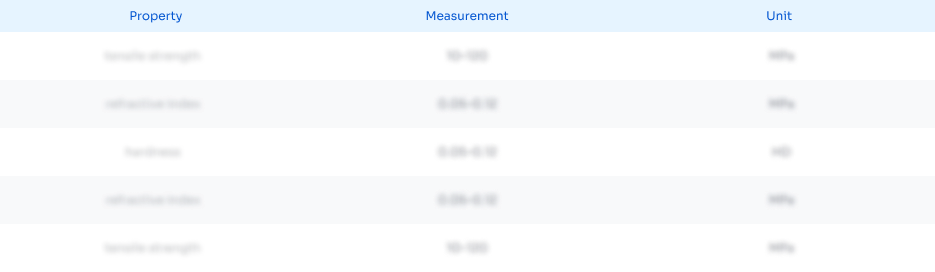
Abstract
Description
Claims
Application Information

- R&D Engineer
- R&D Manager
- IP Professional
- Industry Leading Data Capabilities
- Powerful AI technology
- Patent DNA Extraction
Browse by: Latest US Patents, China's latest patents, Technical Efficacy Thesaurus, Application Domain, Technology Topic, Popular Technical Reports.
© 2024 PatSnap. All rights reserved.Legal|Privacy policy|Modern Slavery Act Transparency Statement|Sitemap|About US| Contact US: help@patsnap.com