Double-buffering casting system for directional hollow turbine work blade
A pouring system and double-buffering technology, applied in the direction of manufacturing tools, metal processing equipment, and equipment for feeding molten metal into molds, etc., to achieve the effects of reducing impact, reducing flow rate, and reducing scrap rate
- Summary
- Abstract
- Description
- Claims
- Application Information
AI Technical Summary
Problems solved by technology
Method used
Image
Examples
Embodiment 1
[0017] A double-buffer pouring system for directional hollow turbine working blades, which consists of circuitous pouring funnel 1, sprue cup 2, upper filter screen, upper disc 3, solid blocking piece 4, hollow tube 5, vertical sprue 6, lower Filter screen, horizontal sprue 7, blade shell cavity 8, center column pipe 9, chassis 10 and exhaust passage 11; the lower end of circuitous pouring funnel 1 is located at the upper end of sprue cup 2, and the lower end of sprue cup 2 is connected to the upper end of sprue cup 2. The discs 3 are connected, the upper surface of the upper disc 3 is connected with the upper end of the vertical sprue 6, the lower surface of the upper disc 3 is connected with a solid block piece 4, and the outer edge of the upper disc 3 has a hollow hole vertically passing through the disc. The tube 5, the lower end side of the vertical sprue 6 is connected to the horizontal sprue 7, the horizontal sprue 7 is connected to the lower end of the blade shell cavit...
PUM
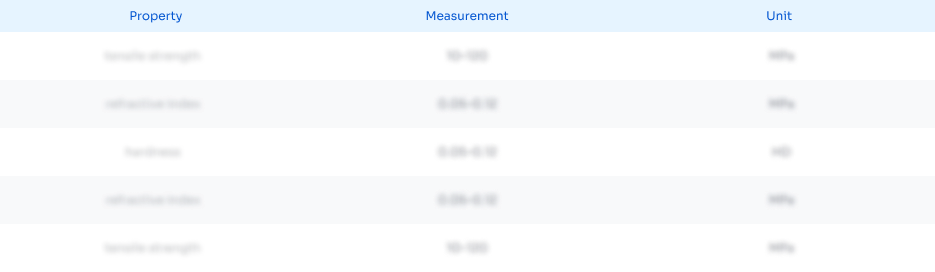
Abstract
Description
Claims
Application Information

- R&D Engineer
- R&D Manager
- IP Professional
- Industry Leading Data Capabilities
- Powerful AI technology
- Patent DNA Extraction
Browse by: Latest US Patents, China's latest patents, Technical Efficacy Thesaurus, Application Domain, Technology Topic, Popular Technical Reports.
© 2024 PatSnap. All rights reserved.Legal|Privacy policy|Modern Slavery Act Transparency Statement|Sitemap|About US| Contact US: help@patsnap.com