Processing method for press roll-shaped structural parts
A processing method and technology for structural parts, applied in the field of machinery, can solve the problems of troublesome manufacturing process, low production efficiency and high processing cost, and achieve the effects of low processing cost, high production efficiency and good product quality.
- Summary
- Abstract
- Description
- Claims
- Application Information
AI Technical Summary
Problems solved by technology
Method used
Examples
Embodiment Construction
[0015] Preferred embodiments of the present invention are described below, and it should be understood that the preferred embodiments described here are only used to illustrate and explain the present invention, and are not intended to limit the present invention.
[0016] According to an embodiment of the present invention, a method for processing a roller-shaped structural member is provided, including:
[0017] Preparatory steps: Based on the fixed bracket to be poured, set up a casting mold, and cast through the casting mold to obtain the required fixed bracket; after calcining and water cooling the casted fixed bracket, polish and polish, and then use a blower to blow off the surface of the fixed bracket grinding dust;
[0018] Step 1: Press the roller-shaped structural member that needs to be equipped with a bracket on the fixed bracket to be poured through the V-shaped elastic sheet; the roller-shaped structural member and the fixed bracket are respectively connected to...
PUM
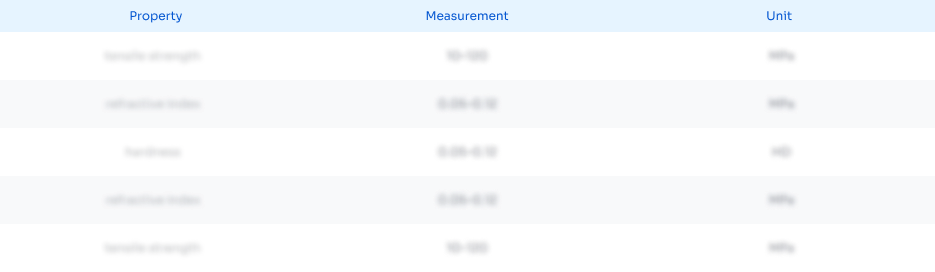
Abstract
Description
Claims
Application Information

- Generate Ideas
- Intellectual Property
- Life Sciences
- Materials
- Tech Scout
- Unparalleled Data Quality
- Higher Quality Content
- 60% Fewer Hallucinations
Browse by: Latest US Patents, China's latest patents, Technical Efficacy Thesaurus, Application Domain, Technology Topic, Popular Technical Reports.
© 2025 PatSnap. All rights reserved.Legal|Privacy policy|Modern Slavery Act Transparency Statement|Sitemap|About US| Contact US: help@patsnap.com