Aluminum alloy diesel engine cylinder cover casting method
A technology of diesel engine and aluminum alloy, which is applied in the direction of casting molding equipment, casting mold, casting mold composition, etc., can solve the problems of not meeting the requirements of rapid casting verification, long manufacturing cycle, high manufacturing cost, etc., so as to achieve no need for mold investment and casting cost low cost effect
- Summary
- Abstract
- Description
- Claims
- Application Information
AI Technical Summary
Problems solved by technology
Method used
Image
Examples
Embodiment Construction
[0026] The specific embodiments of the present invention will be described in detail below in conjunction with the accompanying drawings, but it should be understood that the protection scope of the present invention is not limited by the specific embodiments.
[0027] Unless expressly stated otherwise, throughout the specification and claims, the term "comprise" or variations thereof such as "includes" or "includes" and the like will be understood to include the stated elements or constituents, and not Other elements or other components are not excluded.
[0028] A method for casting an aluminum alloy diesel engine cylinder head according to a specific embodiment of the present invention, comprising the following steps:
[0029] The first step is to process the metal-type module, which is processed by a digital die-free forming machine. The metal-type module includes a plate-shaped metal module 12 and a square metal module 13. As a preferred embodiment, the metal-type module ...
PUM
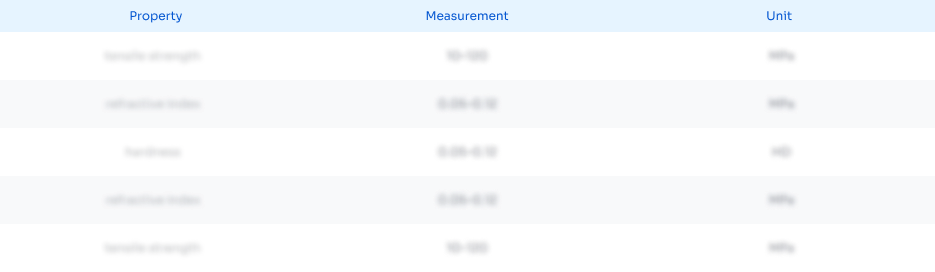
Abstract
Description
Claims
Application Information

- Generate Ideas
- Intellectual Property
- Life Sciences
- Materials
- Tech Scout
- Unparalleled Data Quality
- Higher Quality Content
- 60% Fewer Hallucinations
Browse by: Latest US Patents, China's latest patents, Technical Efficacy Thesaurus, Application Domain, Technology Topic, Popular Technical Reports.
© 2025 PatSnap. All rights reserved.Legal|Privacy policy|Modern Slavery Act Transparency Statement|Sitemap|About US| Contact US: help@patsnap.com