Machining process of roller carrier shaft of belt conveyer
A technology of belt conveyor and processing technology, which is applied in the direction of conveyor objects, rollers, transportation and packaging, etc., to achieve the effects of improving processing efficiency, ensuring roughness, and good thermal workability
- Summary
- Abstract
- Description
- Claims
- Application Information
AI Technical Summary
Problems solved by technology
Method used
Examples
Embodiment 1
[0019] (1) Blank blanking;
[0020] (2) Milling the end face and drilling the center hole: use the idler shaft milling end face drilling center hole machine tool QXZ to mill the end face of the idler shaft, the milling speed is 600~700r / min, the feed rate is controlled at 0.4~0.6mm / r, the drilling The speed is 700~750r / min;
[0021] (3) Rough and fine turning of the outer circle and chamfering: use CA6140 to rough and finish the outer circle of the idler shaft, control the rough turning speed at 600~710r / min, control the feed rate at 0.20~0.30mm / r, The speed of the car is controlled at 850~950r / min, and the feed rate is controlled at 0.10~0.20mm / r;
[0022] (4) Milling shaft flat groove: The idler shaft is processed by XZ36 milling machine, the speed is controlled at 750~850r / min, and the feed rate is controlled at 0.15~0.25mm / r;
[0023] (5) Grinding the outer circle: use the M7625 grinding machine to grind the outer circle of the roller shaft, the speed is controlled at 40...
Embodiment 2
[0025] Embodiment 2: The rest is the same as Embodiment 1, except that the milling speed in step (2) is 600r / min, the feed rate is controlled at 0.4mm / r, and the drilling speed is 700r / min; in step (3) Rough and fine machining the outer circle of the idler shaft, the speed of rough turning is controlled at 600r / min, the feed rate is controlled at 0.20mm / r, the speed of chamfering and finishing is controlled at 850r / min, and the feed rate is controlled at 0.10mm / r; In step (4), the speed of the flat groove of the milling shaft is controlled at 750r / min, and the feed rate is controlled at 0.15mm / r; in step (5), the outer circle of the idler shaft is ground, the speed is controlled at 40m / s, and the feed rate is controlled at 0.010mm / r; step (6) carry out stress-relief annealing on the idler shaft, and control the temperature at 580°C.
Embodiment 3
[0026] Embodiment 3: The rest is the same as in Embodiment 1, except that the milling speed in step (2) is 700r / min, the feed rate is controlled at 0.6mm / r, and the drilling speed is 750r / min; in step (3) Rough and fine machining the outer circle of the idler shaft, the speed of rough turning is controlled at 710r / min, the feed rate is controlled at 0.30mm / r, the speed of chamfering and finishing is controlled at 950r / min, and the feed rate is controlled at 0.20mm / r; In step (4), the speed of the flat groove of the milling shaft is controlled at 850r / min, and the feed rate is controlled at 0.25mm / r; in step (5), the outer circle of the idler shaft is ground, the speed is controlled at 45m / s, and the feed rate is controlled at 0.020mm / r; step (6) carry out stress-relief annealing on the idler shaft, and control the temperature at 650°C.
[0027]
[0028] Example 1 Example 2 Example 3 Radial circular runout (mm) 0.25 0.33 0.34 Curvature (mm / m) 0.3...
PUM
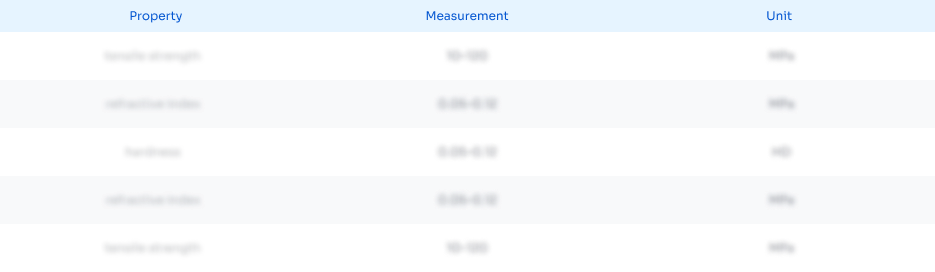
Abstract
Description
Claims
Application Information

- R&D
- Intellectual Property
- Life Sciences
- Materials
- Tech Scout
- Unparalleled Data Quality
- Higher Quality Content
- 60% Fewer Hallucinations
Browse by: Latest US Patents, China's latest patents, Technical Efficacy Thesaurus, Application Domain, Technology Topic, Popular Technical Reports.
© 2025 PatSnap. All rights reserved.Legal|Privacy policy|Modern Slavery Act Transparency Statement|Sitemap|About US| Contact US: help@patsnap.com