Tundish for vacuum smelting furnace casting
A vacuum smelting furnace and tundish technology, which is applied in the direction of casting melt containers, manufacturing tools, metal processing equipment, etc., can solve problems such as difficult temperature control, uneven flow rate, damage to water-cooled ingot molds, etc., to solve product crystallization deviation Coarse, refined alloy crystals, the effect of reducing production costs
- Summary
- Abstract
- Description
- Claims
- Application Information
AI Technical Summary
Problems solved by technology
Method used
Image
Examples
Embodiment 1
[0017] Example 1: The tundish is formed and sintered with alumina and quartz crushed stone. The outer diameter of the body is 140mm, the inner diameter is 130mm, and the height is 50mm. There is a hemispherical slow-filling bag at the center with a radius of 25mm. With the center point of the buffer bag as the center, draw a cross line, On the cross line, 45mm from the center point is the center of the circle, and four leak holes with a diameter of 30mm are made. In the process of use, the alloy liquid flows into the hemispherical slow filling bag in the tundish during pouring, and the alloy liquid forms a secondary natural pouring distribution and enters the four leakage holes and naturally enters the water-cooled ingot mold. Because the bottom of the tundish is designed to have a concave arc , the alloy liquid left between the leakage holes flows into the leakage hole along the concave bottom, and finally flows into the water-cooled ingot mold, which can solve the problems of...
PUM
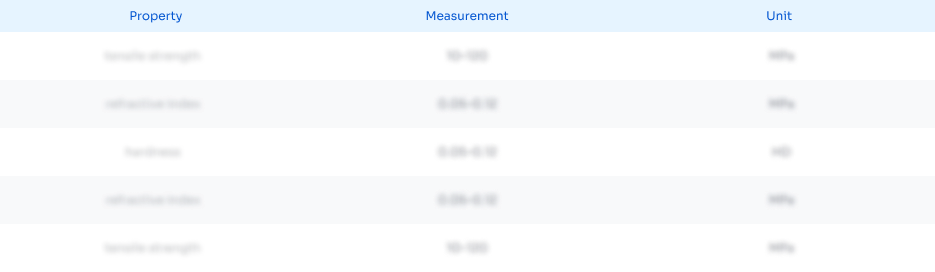
Abstract
Description
Claims
Application Information

- Generate Ideas
- Intellectual Property
- Life Sciences
- Materials
- Tech Scout
- Unparalleled Data Quality
- Higher Quality Content
- 60% Fewer Hallucinations
Browse by: Latest US Patents, China's latest patents, Technical Efficacy Thesaurus, Application Domain, Technology Topic, Popular Technical Reports.
© 2025 PatSnap. All rights reserved.Legal|Privacy policy|Modern Slavery Act Transparency Statement|Sitemap|About US| Contact US: help@patsnap.com