Method for manufacturing variable-pitch optical grating
A variable pitch grating and manufacturing method technology, applied in the field of spectroscopy, can solve problems such as the collapse of photoresist grooves, the impact of grating technical indicators, and difficult control of process conditions, achieving low cost, controllable process, and shortened production cycle Effect
- Summary
- Abstract
- Description
- Claims
- Application Information
AI Technical Summary
Problems solved by technology
Method used
Image
Examples
specific Embodiment approach 1
[0014] Specific implementation mode 1. Combination figure 1 with figure 2 Illustrate the present embodiment, the manufacture method of variable pitch grating, this method is realized by the following steps:
[0015] Substrate cleaning 1: The grating substrate should be single crystal silicon with no bubbles, no scratches, and polished, and clean the grating substrate with a cleaning solution such as acetone to ensure that the surface of the substrate is clean, dense and dry, so as to facilitate the contact between the photoresist and the surface of the substrate. Adhesion.
[0016] Coating 2: Apply photoresist on the cleaned grating substrate, and use the rotation method to uniform the coating, that is, drop the photoresist on the grating substrate, and obtain a uniform photoresist film by centrifugal rotation. The thickness of the glue layer is mainly controlled by the rotation speed during glue spreading, the higher the speed is, the thinner the glue layer is, and the low...
specific Embodiment approach 2
[0025] Specific embodiment two, combine figure 1 with figure 2 Describe this implementation mode, this implementation mode is an embodiment of the manufacturing method of the variable pitch grating described in the first specific implementation mode:
[0026] 1. Clean the polished monocrystalline silicon substrate without bubbles and scratches with a cleaning solution such as acetone;
[0027] 2. Coating photoresist on the monocrystalline silicon substrate, the photoresist is Shiply1805 positive photoresist, the rotation speed is controlled at 1700-5000 rpm during coating, and the coating time is not less than 30 seconds. This can ensure the full volatilization of the solvent and the uniformity of the thickness of the film. The thickness of the coating is 300-700nm.
[0028] 3. Put the photoresist-coated grating substrate into the oven for pre-baking, raise the temperature of the oven to 90°C, and take it out after 30 minutes;
[0029] 4. Expose the grating substrate in th...
PUM
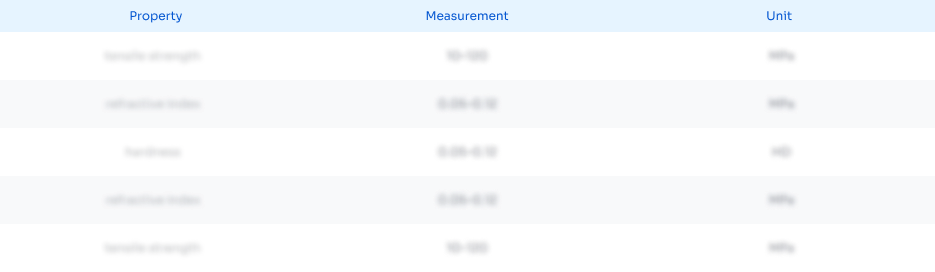
Abstract
Description
Claims
Application Information

- R&D Engineer
- R&D Manager
- IP Professional
- Industry Leading Data Capabilities
- Powerful AI technology
- Patent DNA Extraction
Browse by: Latest US Patents, China's latest patents, Technical Efficacy Thesaurus, Application Domain, Technology Topic, Popular Technical Reports.
© 2024 PatSnap. All rights reserved.Legal|Privacy policy|Modern Slavery Act Transparency Statement|Sitemap|About US| Contact US: help@patsnap.com