Preparation method for rubber for inner rubber layer of car power steering hose
A technology of power steering tube and inner rubber layer, applied in the field of rubber parts for automobiles, can solve problems such as poor heat resistance, and achieve the effect of improving heat resistance
- Summary
- Abstract
- Description
- Claims
- Application Information
AI Technical Summary
Problems solved by technology
Method used
Examples
Embodiment 1
[0014] The rubber used for the inner rubber layer of the automobile power steering tube adopts the following raw materials: 10.0kg of chlorosulfonated polyethylene; 1.5kg of quick-pressed carbon black; 2.0kg of thermal carbon black; 1.0kg of magnesium oxide; Zinc formate 0.1kg; dilauryl thiodipropionate 0.2kg; zinc stearate 0.1kg; 2,2'-dithiodibenzothiazole 0.5kg; thiocyanate 0.05kg; trimellitic acid Trioctyl ester 1.5kg; Magnesium strong powder 0.5kg; Sulfur 0.02kg;
[0015] Its preparation method comprises the following steps:
[0016] A. Chlorosulfonated polyethylene, fast extruded carbon black, thermal black, magnesium oxide, zinc diethyldithiocarbamate, dilauryl thiodipropionate, stearic acid in the above raw materials Zinc, 2, 2'-dithiodibenzothiazole, trioctyl trimellitate and magnesium powder are placed in the internal mixer for internal mixing, and after the internal mixing is completed, the glue temperature is 160°C Glue removal to prepare masterbatch;
[0017] B....
Embodiment 2
[0020] The rubber used for the inner rubber layer of the automobile power steering tube adopts the following raw materials: 10.0kg of chlorosulfonated polyethylene; 1.2kg of quick-pressed carbon black; 2.2kg of thermal carbon black; 0.8kg of magnesium oxide; Zinc formate 0.15kg; dilauryl thiodipropionate 0.15kg; zinc stearate 0.2kg; 2,2'-dithiodibenzothiazole 0.4kg; thiocyanate 0.07kg; trimellitic acid Trioctyl ester 1.3kg; Magnesium strong powder 0.7kg; Sulfur 0.01kg;
[0021] Its preparation method comprises the following steps:
[0022] A. Chlorosulfonated polyethylene, fast extruded carbon black, thermal black, magnesium oxide, zinc diethyldithiocarbamate, dilauryl thiodipropionate, stearic acid in the above raw materials Zinc, 2, 2'-dithiodibenzothiazole, trioctyl trimellitate and magnesium powder are placed in the internal mixer for internal mixing, and after the internal mixing is completed, the glue temperature is 160°C Glue removal to prepare masterbatch;
[0023] ...
Embodiment 3
[0026] The rubber used for the inner rubber layer of the automobile power steering tube adopts the following raw materials: 10.0kg of chlorosulfonated polyethylene; 1.0kg of quick-pressed carbon black; 2.5kg of thermal carbon black; 0.5kg of magnesium oxide; Zinc formate 0.2kg; dilauryl thiodipropionate 0.1kg; zinc stearate 0.3kg; 2,2'-dithiodibenzothiazole 0.3kg; thiocyanate 0.08kg; trimellitic acid Trioctyl ester 1.0kg; Magnesium strong powder 1.0kg; Sulfur 0.01kg;
[0027] Its preparation method comprises the following steps:
[0028] A. Chlorosulfonated polyethylene, fast extruded carbon black, thermal black, magnesium oxide, zinc diethyldithiocarbamate, dilauryl thiodipropionate, stearic acid in the above raw materials Zinc, 2, 2'-dithiodibenzothiazole, trioctyl trimellitate and magnesium powder are placed in the internal mixer for internal mixing, and after the internal mixing is completed, the glue temperature is 160°C Glue removal to prepare masterbatch;
[0029] B....
PUM
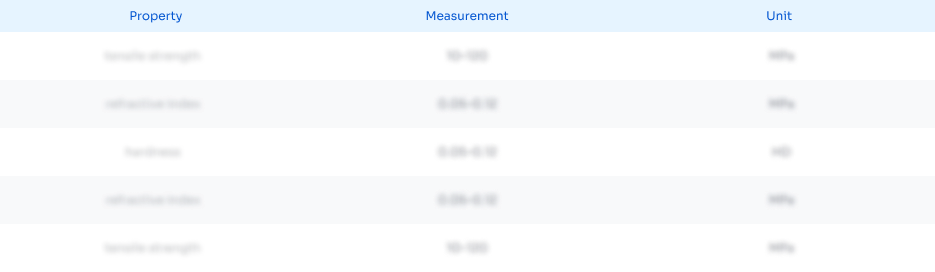
Abstract
Description
Claims
Application Information

- Generate Ideas
- Intellectual Property
- Life Sciences
- Materials
- Tech Scout
- Unparalleled Data Quality
- Higher Quality Content
- 60% Fewer Hallucinations
Browse by: Latest US Patents, China's latest patents, Technical Efficacy Thesaurus, Application Domain, Technology Topic, Popular Technical Reports.
© 2025 PatSnap. All rights reserved.Legal|Privacy policy|Modern Slavery Act Transparency Statement|Sitemap|About US| Contact US: help@patsnap.com