Energy-saving thermal insulation concrete block for building and preparation method thereof
A technology for thermal insulation concrete and construction, applied in the field of building materials, can solve the problems of poor comprehensive performance of foam concrete, long production process cycle, delamination phenomenon, etc., and achieve obvious economic and social benefits, low cost of raw materials, and maintenance time. short effect
- Summary
- Abstract
- Description
- Claims
- Application Information
AI Technical Summary
Problems solved by technology
Method used
Image
Examples
Embodiment 1
[0017] Embodiment 1: a, 10 kilograms of palygorskite and 4 kilograms of pyrophyllite are respectively made into powders with a fineness of 600 to 620 m2 / kg, and 7 kilograms of barite are made into powders with a fineness of 450 to 480 m2 / kg The powder is added to 52 kg of water and stirred at a speed of 600 to 800 rpm for 5 minutes;
[0018] b. Add 75 kg of ordinary portland cement, 35 kg of waste paper, 10 kg of polyimide fibers with a fiber length of 6-8 mm, and 6 kg of lithium phosphate into the mixture in step a at 800-1000 rpm Stir at high speed for 10 minutes;
[0019] c. Quickly add 3 kg of polycarboxylate high-performance water reducer, 2 kg of sodium bicarbonate, 5 kg of sodium dioctyl succinic acid sulfonate, and 2 kg of diisopropyl azodicarboxylate into the mixture in step c, and Stir for 15 minutes at a speed of 400-500 rpm; the polycarboxylate high-performance water reducer is Zhengzhou Aer Building Materials GOR type polycarboxylate high-performance water reduce...
Embodiment 2
[0021] Embodiment 2: a, 9 kilograms of palygorskite and 4 kilograms of pyrophyllite are respectively made into powders whose fineness is 600~620 m2 / kg, and 7 kilograms of barite are made into fineness of 450~480 m2 / kg powder, add the above powder into 45 kg of water, and stir for 5 minutes at a speed of 600-800 rpm;
[0022] b. Add 60 kg of ordinary Portland cement, 30 kg of waste paper, 9 kg of polyimide fibers with a fiber length of 6-8 mm, and 6 kg of lithium phosphate into the mixture in step a at 800-1000 rpm Stir at high speed for 10 minutes;
[0023] c. Quickly add 3 kg of polycarboxylate high-performance water reducer, 2 kg of sodium bicarbonate, 4 kg of sodium dioctyl succinate sulfonate, and 1 kg of diisopropyl azodicarboxylate into the mixture in step c, and Stir for 15 minutes at a speed of 400-500 rpm; the polycarboxylate high-performance water reducer is Zhengzhou Aer Building Materials GOR type polycarboxylate high-performance water reducer;
[0024] d. After ...
Embodiment 3
[0025] Embodiment 3: a, 12 kilograms of palygorskite and 5 kilograms of pyrophyllite are respectively made into powders whose fineness is 600~620 m2 / kg, and 9 kilograms of barite are made into fineness of 450~480 m2 / kg powder, add the above powder into 65 kg of water, and stir for 5 minutes at a speed of 600-800 rpm;
[0026] b. Add 80 kg of ordinary Portland cement, 40 kg of waste paper, 12 kg of polyimide fibers with a fiber length of 6 to 8 mm, and 8 kg of lithium phosphate into the mixture in step a at 800 to 1000 rpm Stir at high speed for 10 minutes;
[0027] c. Quickly add 4 kg of polycarboxylate high-performance water reducer, 3 kg of sodium bicarbonate, 5 kg of dioctyl sodium sulfosuccinate, and 2 kg of diisopropyl azodicarboxylate to the mixture in step c, and Stir for 15 minutes at a speed of 400-500 rpm; the polycarboxylate high-performance water reducer is Zhengzhou Aer Building Materials GOR type polycarboxylate high-performance water reducer;
[0028] d. After...
PUM
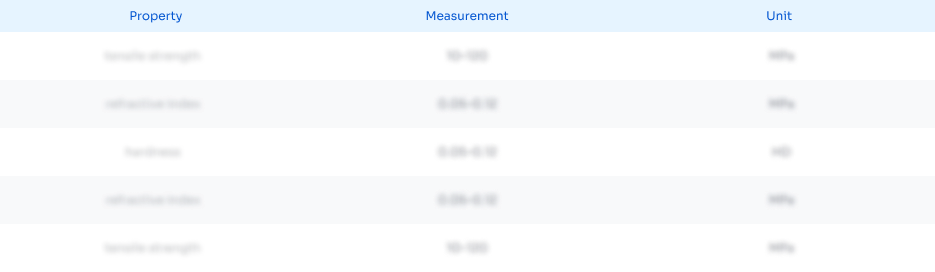
Abstract
Description
Claims
Application Information

- R&D
- Intellectual Property
- Life Sciences
- Materials
- Tech Scout
- Unparalleled Data Quality
- Higher Quality Content
- 60% Fewer Hallucinations
Browse by: Latest US Patents, China's latest patents, Technical Efficacy Thesaurus, Application Domain, Technology Topic, Popular Technical Reports.
© 2025 PatSnap. All rights reserved.Legal|Privacy policy|Modern Slavery Act Transparency Statement|Sitemap|About US| Contact US: help@patsnap.com