Permanent magnet synchronous motor speed composite control method based on continuous terminal slip form technology
A permanent magnet synchronous motor and terminal sliding mode technology, which is applied in the direction of motor generator control, electronic commutation motor control, control system, etc., can solve the problems that cannot meet the control accuracy of the system, and achieve faster convergence speed, faster convergence speed, The effect of improving the response speed
- Summary
- Abstract
- Description
- Claims
- Application Information
AI Technical Summary
Problems solved by technology
Method used
Image
Examples
Embodiment Construction
[0040] In order to make the object, technical solution and advantages of the present invention clearer, the present invention will be further described in detail below in conjunction with the accompanying drawings and embodiments. It should be understood that the specific embodiments described here are only used to explain the present invention, not to limit the present invention. In addition, the technical features involved in the various embodiments of the present invention described below can be combined with each other as long as they do not constitute a conflict with each other.
[0041] A kind of permanent magnet synchronous motor speed composite control method based on continuous terminal sliding mode technology implemented by the present invention comprises the following steps:
[0042] Step (1): collect the three-phase current i on the stator winding a i b i c , through the Clark transformation, converted into the equivalent current i of the α and β axes in the sta...
PUM
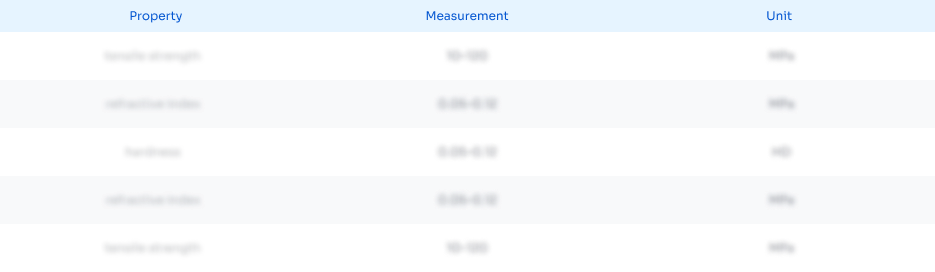
Abstract
Description
Claims
Application Information

- R&D Engineer
- R&D Manager
- IP Professional
- Industry Leading Data Capabilities
- Powerful AI technology
- Patent DNA Extraction
Browse by: Latest US Patents, China's latest patents, Technical Efficacy Thesaurus, Application Domain, Technology Topic, Popular Technical Reports.
© 2024 PatSnap. All rights reserved.Legal|Privacy policy|Modern Slavery Act Transparency Statement|Sitemap|About US| Contact US: help@patsnap.com