Self-adaptation dynamic sliding mode controlling method controlled by virtual axis lathe parallel connection mechanism motion
A virtual axis machine tool and self-adaptive technology, which is applied in the field of virtual axis machine tools, can solve the problems of system control quality degradation, adverse effects of fast-changing dynamic characteristics on system control performance, and system control performance degradation, so as to improve motion control performance and weaken the Adverse effects, effects of increasing resistance
- Summary
- Abstract
- Description
- Claims
- Application Information
AI Technical Summary
Problems solved by technology
Method used
Image
Examples
Embodiment
[0081] The Fangming control method mainly focuses on solving the high-performance control problem of the parallel mechanism motion of the virtual axis machine tool with a new adaptive dynamic sliding mode control technology. Assuming that the virtual axis machine tool is composed of 6 branch parallel mechanisms, driven by AC servo motors, the block diagram of the branch control system is shown in figure 1 shown. The specific implementation of this control method is as follows:
[0082] 1. Establish the mathematical model of the controlled object in each control branch of the virtual axis machine tool with the interference item of the motor drive shaft
[0083] The key to establishing the mathematical model of the controlled object in each control branch of the virtual axis machine tool is to determine the f( x ) and g( x ) . Each branch takes the motor driver and the motor as the controlled objects, takes the parallel mechanism of the virtual axis machine tool as the load,...
PUM
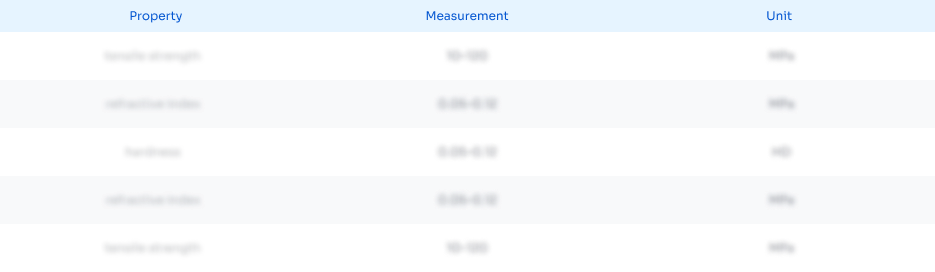
Abstract
Description
Claims
Application Information

- R&D
- Intellectual Property
- Life Sciences
- Materials
- Tech Scout
- Unparalleled Data Quality
- Higher Quality Content
- 60% Fewer Hallucinations
Browse by: Latest US Patents, China's latest patents, Technical Efficacy Thesaurus, Application Domain, Technology Topic, Popular Technical Reports.
© 2025 PatSnap. All rights reserved.Legal|Privacy policy|Modern Slavery Act Transparency Statement|Sitemap|About US| Contact US: help@patsnap.com