Method for preparing magnesium alloy by electrolysis using magnesium oxide as raw material
A magnesium oxide and magnesium alloy technology, applied in the preparation of magnesium alloys, using magnesium oxide as a raw material to electrolytically prepare magnesium alloys, can solve the problems of restricting the commercialization of magnesium alloys, difficulty in continuous production, complicated process, etc., and achieve low cost , small component segregation, simple process
- Summary
- Abstract
- Description
- Claims
- Application Information
AI Technical Summary
Problems solved by technology
Method used
Image
Examples
Embodiment 1
[0098] Mix 2.61g of magnesium oxide, 80.04g of lithium chloride monohydrate, 56.19g of potassium chloride, 3.18g of calcium fluoride and 28.20g of ammonium chloride into a 200mL crucible. After the crucible is covered with a lid, it is incubated at 300°C for 1.5 hours, then at 500°C for 0.5 hour, and the melt containing anhydrous magnesium chloride and anhydrous lithium chloride (the melt composition is: KCl (45.10wt.%) )-(2.26wt.%)NaCl-MgCl 2 (4.98wt.%)-LiCl(45.10wt.%)-CaF 2 (3.18 wt.%)). The melt was very pure and no impurities were observed. Then, the melt is electrolyzed in an electrolytic cell, wherein the electrolysis conditions are: the melt is an electrolyte, the spectrally pure graphite rod of Φ6mm is an anode, the steel wire of Φ1mm is a negative electrode, and a graphite crucible with a volume of 200mL is an electrolytic cell. The electrolysis temperature is 440°C, the pole distance is 4cm, and the cathode current density is 5.4A / cm 2 , the tank voltage is 8.3-8...
Embodiment 2
[0101] 6.97g magnesium oxide, 26.30g lithium chloride hydrate (LiCl 0.5H 2 (2), 43.40g potassium chloride, 2.17g sodium chloride, 4.02g calcium fluoride and 40.30g ammonium chloride are mixed and added in a 200mL crucible. After the crucible was covered with a lid, it was incubated at 300°C for 2 hours, then at 480°C for 1 hour, and a melt containing anhydrous magnesium chloride and anhydrous lithium chloride was obtained (melt composition: KCl (39.61wt.%) )-NaCl(1.98wt.%)-MgCl 2(15.13wt.%)-LiCl(39.61wt.%)-CaF 2 (3.67 wt.%)). The melt was very pure and no impurities were observed. Then, the melt is electrolyzed in an electrolytic cell, wherein the electrolysis conditions are: the melt is an electrolyte, the spectrally pure graphite rod of Φ6mm is an anode, the steel wire of Φ1mm is a negative electrode, and a graphite crucible with a volume of 200mL is an electrolytic cell. The electrolysis temperature is 480°C, the pole distance is 4cm, and the cathode current density is ...
Embodiment 3
[0105] Mix 14.00g of magnesium oxide, 100.00g of potassium chloride, 11.40g of lanthanum chloride heptahydrate, 4.88g of calcium fluoride and 66.24g of ammonium chloride into a 200mL crucible. After the crucible was covered with a lid, it was incubated at 400° C. for 1.5 hours, and then at 700° C. for 1 hour to obtain a melt containing anhydrous magnesium chloride and anhydrous lanthanum chloride (melt composition: KCl (68.65wt.%) )-MgCl 2 (23.14wt.%)-LaCl 3 (5.17wt.%)-CaF 2 (3.35wt.%)), the melt is very pure, no impurities can be observed. Then, the melt is electrolyzed in an electrolytic cell, wherein the electrolysis conditions are: the melt is an electrolyte, the spectrally pure graphite rod of Φ6mm is an anode, the steel wire of Φ1mm is a negative electrode, and a graphite crucible with a volume of 200mL is an electrolytic cell. The electrolysis temperature is 690°C, the pole distance is 4cm, and the cathode current density is 6.3A / cm 2 , the tank voltage is 7.9-8.3V,...
PUM
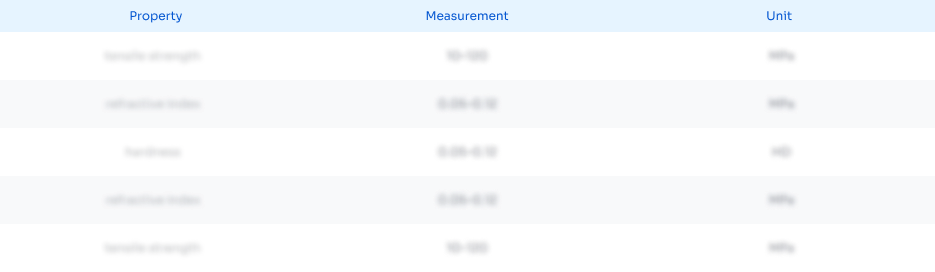
Abstract
Description
Claims
Application Information

- R&D
- Intellectual Property
- Life Sciences
- Materials
- Tech Scout
- Unparalleled Data Quality
- Higher Quality Content
- 60% Fewer Hallucinations
Browse by: Latest US Patents, China's latest patents, Technical Efficacy Thesaurus, Application Domain, Technology Topic, Popular Technical Reports.
© 2025 PatSnap. All rights reserved.Legal|Privacy policy|Modern Slavery Act Transparency Statement|Sitemap|About US| Contact US: help@patsnap.com