Novel fine mixed leather finished product sorting method
A finished product and a new type of technology, applied in the field of fur finishing, can solve the problems of high labor intensity, cumbersome operation and long cycle, and achieve the effect of reducing labor intensity, improving processing efficiency and reducing processing cost.
- Summary
- Abstract
- Description
- Claims
- Application Information
AI Technical Summary
Problems solved by technology
Method used
Examples
Embodiment 1
[0009] In the finishing method of the new fine leather finished products described in this embodiment, the finishing equipment adopts a shrinking machine, and the shrinking machine is placed in a closed outer room; According to the processing requirements, the same type of fur meets the above four requirements; put the finished product of the same type of fine miscellaneous skin into the shrinking machine, close the drum door, and close the door of the airtight outer room, and then start the shrinking machine, so that Turn the shrinking machine; open the intake valve on the shrinking machine, inject steam into the shrinking machine until the temperature inside the shrinking machine reaches 60°C, close the intake valve, and continue to rotate for 20 minutes; open the door of the airtight outer room, When the internal temperature of the shrinking machine drops to 60°C, turn on the feeding switch on the shrinking machine, and spray the brightener evenly inside the shrinking machin...
Embodiment 2
[0011] In the finishing method of the new fine leather finished products described in this embodiment, the finishing equipment adopts a shrinking machine, and the shrinking machine is placed in a closed outer room; According to the processing requirements, the same type of fur meets the above four requirements; put the finished product of the same type of fine miscellaneous skin into the shrinking machine, close the drum door, and close the door of the airtight outer room, and then start the shrinking machine, so that Turn the shrinking machine; open the intake valve on the shrinking machine, inject steam into the shrinking machine until the temperature inside the shrinking machine reaches 95°C, close the intake valve, and continue to rotate for 30 minutes; open the door of the airtight outer room, When the internal temperature of the shrinking machine drops to 85°C, turn on the feeding switch on the shrinking machine, and spray the brightener evenly inside the shrinking machin...
Embodiment 3
[0013] In the finishing method of the new fine leather finished products described in this embodiment, the finishing equipment adopts a shrinking machine, and the shrinking machine is placed in a closed outer room; According to the processing requirements, the same type of fur meets the above four requirements; put the finished product of the same type of fine miscellaneous skin into the shrinking machine, close the drum door, and close the door of the airtight outer room, and then start the shrinking machine, so that Turn the shrinking machine; open the intake valve on the shrinking machine, inject steam into the shrinking machine until the temperature inside the shrinking machine reaches 85°C, close the intake valve, and continue to rotate for 25 minutes; open the door of the airtight outer room, When the internal temperature of the shrinking machine drops to 75°C, turn on the feeding switch on the shrinking machine, and spray the brightener evenly inside the shrinking machin...
PUM
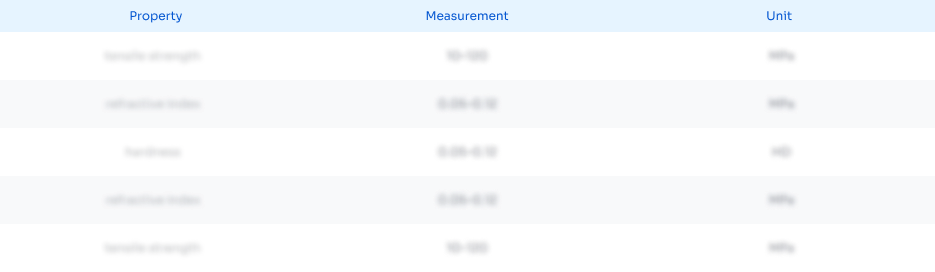
Abstract
Description
Claims
Application Information

- R&D Engineer
- R&D Manager
- IP Professional
- Industry Leading Data Capabilities
- Powerful AI technology
- Patent DNA Extraction
Browse by: Latest US Patents, China's latest patents, Technical Efficacy Thesaurus, Application Domain, Technology Topic, Popular Technical Reports.
© 2024 PatSnap. All rights reserved.Legal|Privacy policy|Modern Slavery Act Transparency Statement|Sitemap|About US| Contact US: help@patsnap.com