Beneficiation method for color molybdenum lead ores
A technology of colored molybdenum lead ore and ore dressing method, which is applied in the direction of chemical instruments and methods, flotation, wet separation, etc., and can solve complex process flow, low molybdenum concentrate grade and recovery rate, activator and collector agent Large consumption and other problems, to achieve the effect of simple process, easy large-scale production, and low cost
- Summary
- Abstract
- Description
- Claims
- Application Information
AI Technical Summary
Problems solved by technology
Method used
Image
Examples
Embodiment 1
[0022] The colored molybdenum ore is subjected to magnetic separation with a magnetic field strength of 1.5T to remove magnetic minerals and obtain non-magnetic
[0023] sexual minerals. Add sodium carbonate according to the dosage in Table 1, the grinding concentration is 50%, and the non-magnetic minerals are ground to
[0024] -0.074mm accounts for 52%; the non-magnetic minerals after grinding are removed from the -5μm difficult-to-recover slime, and after desliming, water is added to adjust the slurry to a concentration of 33%; the following is as listed in Table 1. Slurry, roughing, and selection Operate with the dosage of scanning agent. The pH value of the slurry after pulping is 10: one roughing, three beneficiation and three sweeping, the first beneficiation concentration is 16%, the second beneficiation concentration is 12%, the third beneficiation concentration is 8%, and the sweeping The concentration is 28%, the medium ore and the sweeping ore are returned to th...
Embodiment 2
[0026] Magnetic separation is the same as in Example 1. Add sodium carbonate to the non-magnetic minerals according to the amount in Table 1, the grinding concentration is 55%, and the grinding to -0.074mm accounts for 65%; the non-magnetic minerals after grinding are removed -5μm is difficult to recover the slime, after desliming Add water to adjust the slurry to a concentration of 30%; operate according to the dosage of slurry, roughing, selecting and sweeping listed in Table 1. The pH value of the slurry after pulping is 10.6: first roughing, three times of beneficiation and three times of sweeping, the first beneficiation concentration is 15%, the second beneficiation concentration is 10%, the third beneficiation concentration is 6%, and the sweeping The concentration is 27%, the medium ore and the sweeping ore return to the previous operation in sequence to form a closed circuit; the flotation concentrate is separated by shaking table gravity separation, and the gravity m...
Embodiment 3
[0028] Magnetic separation is the same as in Example 1. Add sodium carbonate to the non-magnetic minerals according to the amount in Table 1, the grinding concentration is 60%, and the grinding to -0.074mm accounts for 55%; the non-magnetic minerals after grinding are removed -5μm is difficult to recover the slime, after desliming Add water to adjust the slurry to a concentration of 33%; operate according to the dosage of slurry, roughing, selecting and sweeping listed in Table 1. The pH value of the slurry after pulping is 12: first roughing, three times of beneficiation and three times of sweeping, the first beneficiation concentration is 18%, the second beneficiation concentration is 12%, the third beneficiation concentration is 7%, and the sweeping The concentration is 28%, the medium ore and the sweeping ore return to the previous operation in sequence to form a closed loop; the flotation concentrate is separated by shaking table gravity separation, and the gravity molybd...
PUM
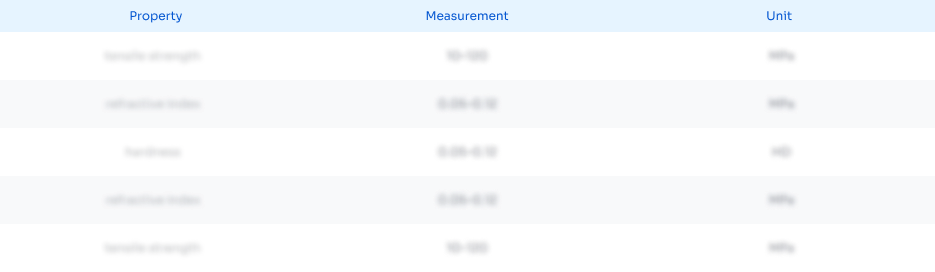
Abstract
Description
Claims
Application Information

- R&D
- Intellectual Property
- Life Sciences
- Materials
- Tech Scout
- Unparalleled Data Quality
- Higher Quality Content
- 60% Fewer Hallucinations
Browse by: Latest US Patents, China's latest patents, Technical Efficacy Thesaurus, Application Domain, Technology Topic, Popular Technical Reports.
© 2025 PatSnap. All rights reserved.Legal|Privacy policy|Modern Slavery Act Transparency Statement|Sitemap|About US| Contact US: help@patsnap.com