Sintering energy-saving technique and system capable of removing multiple pollutants
A pollutant removal technology, applied in the direction of dispersed particle separation, air quality improvement, chemical instruments and methods, etc., can solve the problem of not being able to properly divide the concentration area of pollutants, and failing to make good use of sintering machine head smoke Gas waste heat, can not be well dealt with and other issues, to achieve the effect of reducing initial investment and operating costs, compact structure, and reduce production
- Summary
- Abstract
- Description
- Claims
- Application Information
AI Technical Summary
Problems solved by technology
Method used
Image
Examples
Embodiment Construction
[0039] Such as figure 1 As shown, the sintering energy-saving and multiple pollutants removal system in this embodiment includes a sintering machine 104, a sintering bellows 107, an ignition device 103, a circulating fume hood 105, a blower 106, a section A induced draft fan 101, a chimney 100, Bag dust collector 102, rotary preheater 113 and rotary preheater 114, afterburner burner 112, ammonia injection device 110, SCR denitrification device 111, desulfurization device 109, B-section induced draft fan 115, B-section circulation fan 116 , C section induced draft fan 117, sintering cooler 203, cooler high temperature section 201, cooler low temperature section 202, cooler blower 200, low temperature section circulation fan 204 and induced draft fan 108.
[0040] The sintering bellows 107 are located at the lower part of the sintering machine 104. According to the concentration distribution of pollutants produced during iron ore sintering, the sintering bellows 107 are divided ...
PUM
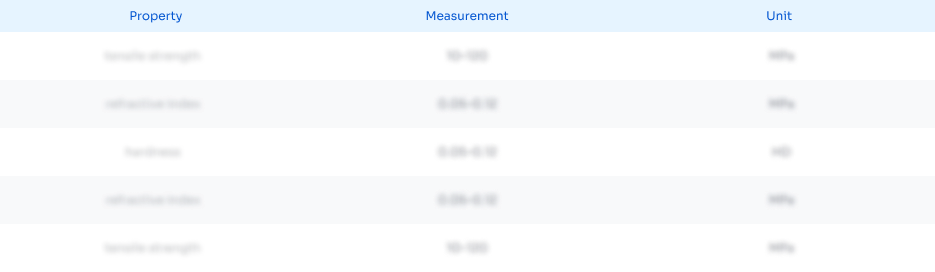
Abstract
Description
Claims
Application Information

- Generate Ideas
- Intellectual Property
- Life Sciences
- Materials
- Tech Scout
- Unparalleled Data Quality
- Higher Quality Content
- 60% Fewer Hallucinations
Browse by: Latest US Patents, China's latest patents, Technical Efficacy Thesaurus, Application Domain, Technology Topic, Popular Technical Reports.
© 2025 PatSnap. All rights reserved.Legal|Privacy policy|Modern Slavery Act Transparency Statement|Sitemap|About US| Contact US: help@patsnap.com