New synthesis technique of 3,5,6-trichloropyridyl-2-sodium alkoxide
A technology of trichloropyridine and synthesis technology, applied in the new synthesis technology field, can solve the problems of many by-products in the one-step addition and cyclization method, being unsuitable for industrial large-scale production, difficult to large-scale production, etc. The effect of improved performance and yield, and low cost of production equipment
- Summary
- Abstract
- Description
- Claims
- Application Information
AI Technical Summary
Problems solved by technology
Method used
Examples
Embodiment 1
[0025] In a 3000L enamel glass reactor, add 546Kg trichloroacetyl chloride, 190.8kg acrylonitrile, 1638kg chlorinated benzene, 2.73Kg cuprous chloride, 5.46Kg copper powder, and control the reflux reaction temperature at 100°C-125°C. After 30 hours, after the addition reaction, cool down to 60°C, add 2.73g of trialkylamine, and react for 4 hours. After the reaction, filter out the catalyst, and remove 3 / 4 of the filtrate at -0.8~0.9MP. Then the remaining liquid is discharged into the crystallization tank, the pyridone solution is cooled and crystallized, separated and dried to obtain pyridone. Mix 1 part of pyridone and 3 parts of water into the alkali analysis kettle, add dropwise 20% NaOH solution, control the reaction temperature not to exceed 50°C, adjust the pH to 11, keep it at 40°C for 2 hours, and then filter to obtain trichloropyridine Sodium alkoxide, the yield is 78%.
Embodiment 2
[0027] In a 3000L enamel glass reaction kettle, add 546Kg trichloroacetyl chloride, 190.8kg acrylonitrile, 1638kg chlorinated benzene, 2.73Kg cuprous chloride, 5.46Kg copper powder, and control the reflux reaction temperature at 100°C-125°C. After 30 hours, after the addition reaction, cool down to 60°C, add 2.73g of pyridine, and react for 4 hours. After the reaction, filter out the catalyst, and remove 3 / 4 of the filtrate at -0.8~0.9MP. Then the remaining liquid is discharged into the crystallization tank, the pyridone solution is cooled and crystallized, separated and dried to obtain pyridone. Mix 1 part of pyridone and 3 parts of water into the alkali analysis kettle, add dropwise 20% NaOH solution, control the reaction temperature not to exceed 50°C, adjust the pH to 11, keep it at 40°C for 2 hours, and then filter to obtain trichloropyridine Sodium alkoxide, the yield is 75%.
Embodiment 3
[0029] In a 3000L enamel glass reaction kettle, add 546Kg trichloroacetyl chloride, 190.8kg acrylonitrile, 1638kg chlorinated benzene, 2.73Kg cuprous chloride, 5.46Kg copper powder, and control the reflux reaction temperature at 100°C-125°C. After 30 hours, after the addition reaction, cool down to 60°C, add 2.73g of lutidine, and react for 4 hours. After the reaction, filter off the catalyst, and remove 3 / 4 of the filtrate at -0.8~0.9MP. Then the remaining liquid is discharged into the crystallization tank, the pyridone solution is cooled and crystallized, separated and dried to obtain pyridone. Mix 1 part of pyridone and 3 parts of water into the alkali analysis kettle, add dropwise 20% NaOH solution, control the reaction temperature not to exceed 50°C, adjust the pH to 11, keep it at 40°C for 2 hours, and then filter to obtain trichloropyridine Sodium alkoxide, the yield is 81%.
PUM
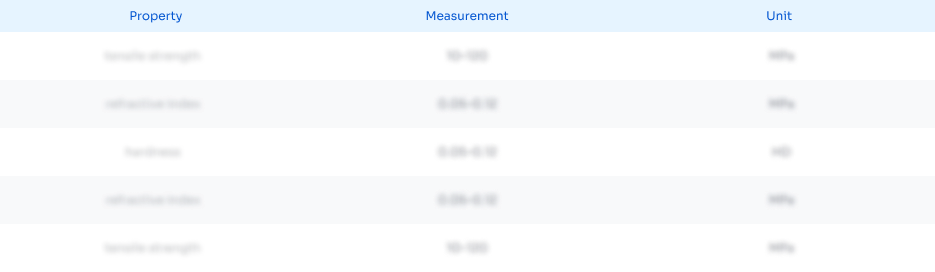
Abstract
Description
Claims
Application Information

- R&D
- Intellectual Property
- Life Sciences
- Materials
- Tech Scout
- Unparalleled Data Quality
- Higher Quality Content
- 60% Fewer Hallucinations
Browse by: Latest US Patents, China's latest patents, Technical Efficacy Thesaurus, Application Domain, Technology Topic, Popular Technical Reports.
© 2025 PatSnap. All rights reserved.Legal|Privacy policy|Modern Slavery Act Transparency Statement|Sitemap|About US| Contact US: help@patsnap.com