Steel ball surface spreading apparatus based on machine vision
A technology of machine vision and steel ball, which is applied in the direction of measuring devices, instruments, scientific instruments, etc., can solve the problem that the steel ball cannot be rolled and unfolded actively, and achieve the effects of easy layout and adjustment, high sorting efficiency, and avoiding missed inspections
- Summary
- Abstract
- Description
- Claims
- Application Information
AI Technical Summary
Problems solved by technology
Method used
Image
Examples
Embodiment 1
[0023] Example 1, see figure 1 Shown:
[0024] A steel ball surface unfolding device based on machine vision. This device is an important component of a steel ball sorter, including a guide rail 2 for carrying steel balls 3, and a screw 1 arranged under the guide rail 2 and rolling with the steel balls 3. And the driving device that drives the screw rod 1 to rotate (the driving device and the screw rod 1 can adopt connection structures such as gears and belts, which belong to known technology, so the driving device is not shown in the figure), the screw rod 1 is provided with a spiral groove that matches the bottom of the steel ball 3, The pitches of the spiral grooves are equal. When the steel ball 3 passes through the guide rail 2 above the screw 1, the steel ball 3 rolls radially and laterally displaces relative to the guide rail 2 under the joint action of the drive of the screw 1 and the guidance of the guide rail 2, and the steel ball 3Roll radially at least one circle....
Embodiment 2
[0030] Example 2, see figure 2 Shown:
[0031] In this embodiment, the surface expansion of the steel ball 3 with a ball diameter of 36 mm is used as an example for illustration, wherein the length of the screw 1 is 180 mm, and the length of the pitch is 20 mm, that is, the length of the screw 1 is 9 times the pitch, and the screw 1 rotates for 2 turns to drive the steel ball. The ball 3 radially rolls 1 / 4 of the circle relative to the guide rail 2 and displaces 2 pitches laterally. The difference between this embodiment and Embodiment 1 is that the ball diameter of the steel ball 3 is greater than 1 times the pitch of the screw 1 but less than 2 times the pitch. Under the action, only after the screw rod 1 rotates for 2 weeks, the next steel ball 3 has space to enter the spiral groove from the front end of the screw rod 1 again. This embodiment shows that: when the ball diameter of the steel ball 3 is greater than N times the pitch but less than N+1 times the pitch, N≥0, t...
Embodiment 3
[0032] Example 3, see image 3 with Figure 4 Shown:
[0033] Embodiment 1 and Embodiment 2 both use a screw rod 1 to drive the steel ball 3, and the image sensor can only pick up an image that goes around the steel ball 3 in one rolling direction, while the image sensor has Therefore, the surface image of the entire steel ball 3 cannot be fully captured. To solve this problem, two images can be added at the position where the steel ball 3 exits from the front end of the screw 1 and the position where the steel ball 3 exits from the rear end of the screw 1. The steel ball 3 at two positions rolls along the guide rail 2, and has a nearly orthogonal angle with the radial rolling of the screw 1, so the image sensor can capture the images of the steel ball 3 at six positions to reconstruct and generate a complete steel ball 3. Image of the surface of the ball 3. However, there is still a certain degree of randomness in the two captured images added by this method, which will af...
PUM
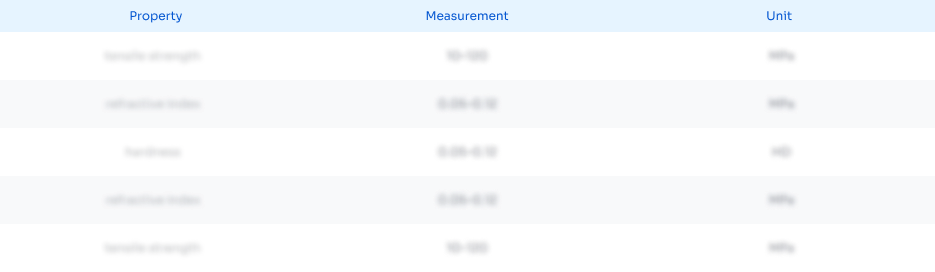
Abstract
Description
Claims
Application Information

- R&D
- Intellectual Property
- Life Sciences
- Materials
- Tech Scout
- Unparalleled Data Quality
- Higher Quality Content
- 60% Fewer Hallucinations
Browse by: Latest US Patents, China's latest patents, Technical Efficacy Thesaurus, Application Domain, Technology Topic, Popular Technical Reports.
© 2025 PatSnap. All rights reserved.Legal|Privacy policy|Modern Slavery Act Transparency Statement|Sitemap|About US| Contact US: help@patsnap.com