Preparation method of desulfurized gypsum foaming cement warming plate
A technology of desulfurized gypsum and foamed cement, applied in ceramic products, sustainable waste treatment, solid waste management, etc., to achieve the effects of good fire safety, good compressive strength and simple process
- Summary
- Abstract
- Description
- Claims
- Application Information
AI Technical Summary
Problems solved by technology
Method used
Examples
Embodiment 1
[0017] Weigh 150kg of ordinary Portland cement, 80kg of fly ash, 5kg of desulfurized gypsum, 0.4kg of water reducer, 0.6kg of polypropylene fiber, 13.0kg of foaming agent, and 0.8kg of composite foam stabilizer. The steps of the production method are as follows: uniformly mixing powder materials: after starting the mixer, adding ordinary Portland cement, fly ash, desulfurized gypsum, water reducing agent, polypropylene fiber and foam stabilizer, and stirring evenly. Add water and stir for 2 to 3 minutes, add foaming agent and stir quickly for 5 to 10 seconds, and immediately foam in the injection mold, curing, demoulding, cutting, and curing of the finished product.
Embodiment 2
[0019] Weigh 170kg of ordinary Portland cement, 70kg of fly ash, 7kg of desulfurized gypsum, 0.6kg of water reducer, 0.8kg of polypropylene fiber, 15.0kg of foaming agent, and 1.0kg of composite foam stabilizer. The steps of the production method are as follows: uniformly mixing powder materials: after starting the mixer, adding ordinary Portland cement, fly ash, desulfurized gypsum, water reducing agent, polypropylene fiber and foam stabilizer, and stirring evenly. Add water and stir for 2 to 3 minutes, add foaming agent and stir quickly for 5 to 10 seconds, and immediately foam in the injection mold, curing, demoulding, cutting, and curing of the finished product.
Embodiment 3
[0021] Weigh 180kg of ordinary Portland cement, 60kg of fly ash, 8kg of desulfurized gypsum, 0.8kg of water reducer, 1.0kg of polypropylene fiber, 16.0kg of foaming agent, and 1.2kg of composite foam stabilizer. The steps of the production method are as follows: uniformly mixing powder materials: after starting the mixer, adding ordinary Portland cement, fly ash, desulfurized gypsum, water reducing agent, polypropylene fiber and foam stabilizer, and stirring evenly. Add water and stir for 2 to 3 minutes, add foaming agent and stir quickly for 5 to 10 seconds, and immediately foam in the injection mold, curing, demoulding, cutting, and curing of the finished product.
PUM
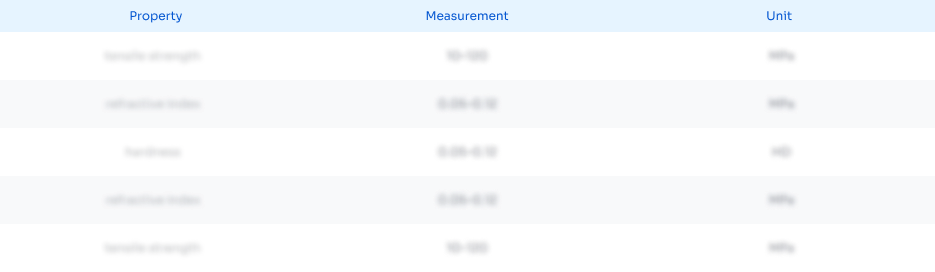
Abstract
Description
Claims
Application Information

- R&D
- Intellectual Property
- Life Sciences
- Materials
- Tech Scout
- Unparalleled Data Quality
- Higher Quality Content
- 60% Fewer Hallucinations
Browse by: Latest US Patents, China's latest patents, Technical Efficacy Thesaurus, Application Domain, Technology Topic, Popular Technical Reports.
© 2025 PatSnap. All rights reserved.Legal|Privacy policy|Modern Slavery Act Transparency Statement|Sitemap|About US| Contact US: help@patsnap.com