Method for manufacturing titanium and titanium alloy bars by means of hot continuous rolling
A titanium alloy, hot continuous rolling technology, applied in the direction of metal rolling, to achieve the effect of high precision and high quality, strong controllability and uniform structure
- Summary
- Abstract
- Description
- Claims
- Application Information
AI Technical Summary
Problems solved by technology
Method used
Image
Examples
Embodiment 1
[0091] Using the above-mentioned hot continuous rolling production line to produce Φ16.0mm titanium alloy rods, the main steps and parameters are as follows:
[0092] a. Heating: keep a forged billet of titanium alloy with a size of 150×150×12000mm at a heating temperature of 900°C for 2 hours;
[0093] b. Rough rolling: rough rolling the heated forged billet, the rolling speed is 0.7m / s, rolling 4 passes, the pass elongation coefficient is 1.2, and the final rolling temperature is controlled at 850°C;
[0094] c. Intermediate rolling: after rough rolling, cut the head of the rolled piece by 50-100mm, then perform intermediate rolling, the rolling speed is 1.2m / s, rolling 6 passes, the elongation coefficient of each pass is 1.3; the final rolling temperature is controlled at 820°C ;
[0095] d. Finish rolling: after the intermediate rolling, the rolled piece is cut to 50-100mm and rolled at a rolling speed of 4.1m / s, rolling 6 times, and the elongation coefficient of each pas...
Embodiment 2~ Embodiment 5
[0099] According to the steps of Example 1, the process parameters are changed to obtain Φ30.0mm pure titanium rods, Φ50.0mm titanium alloy rods, Φ80.0mm titanium alloy rods and Φ90.0mm pure titanium rods. Table 4 lists Φ16 .0mm titanium alloy rod, Φ30.0mm pure titanium rod, Φ50.0mm titanium alloy rod, Φ80.0mm titanium alloy rod and Φ90.0mm pure titanium rod specific production process parameters.
[0100] The titanium rod products produced in Examples 1 to 5 all conform to the diameter, cross-sectional thickness and size tolerance of titanium and titanium alloy rods specified in the GB / T2965-2007 standard.
[0101] Table 4 Specific process parameters of bars with different specifications
[0102]
PUM
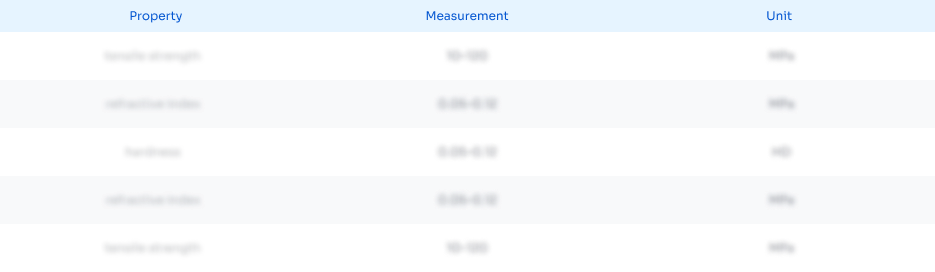
Abstract
Description
Claims
Application Information

- R&D
- Intellectual Property
- Life Sciences
- Materials
- Tech Scout
- Unparalleled Data Quality
- Higher Quality Content
- 60% Fewer Hallucinations
Browse by: Latest US Patents, China's latest patents, Technical Efficacy Thesaurus, Application Domain, Technology Topic, Popular Technical Reports.
© 2025 PatSnap. All rights reserved.Legal|Privacy policy|Modern Slavery Act Transparency Statement|Sitemap|About US| Contact US: help@patsnap.com