Impact-resistant steel ball for ball mill
An impact-resistant, ball mill technology, applied in furnaces, heat treatment equipment, heat treatment furnaces, etc., can solve the problems of high cost, wear resistance can not meet the grinding requirements, etc., to achieve the effect of improving comprehensive performance and optimizing the preparation process
- Summary
- Abstract
- Description
- Claims
- Application Information
AI Technical Summary
Problems solved by technology
Method used
Examples
Embodiment 1
[0020] An impact-resistant steel ball for a ball mill, the weight percentage of each component is as follows:
[0021] C: 0.70%; Si: 0.25%; Cr: 2.0%; Mn: 0.7%; Ni: 0.25%; Ti: 0.050%; Al: 0.9%; W: 0.08%; Mo: 0.20%; S: 0.010%; P: 0.02%; the remainder is Fe;
[0022] During the preparation process, the impact-resistant steel balls for the ball mill were prepared according to the following process steps:
[0023] S1: Weigh the raw materials according to the weight percentage of each component for smelting, carry out refining in the refining device, and carry out final deoxidation in the later stage of refining, pouring, after casting and forming, cleaning to obtain castings;
[0024] S2: Keep the casting obtained in S1 at 860°C for 3 hours, then quench it in water, raise the temperature of the quenched casting to 250°C for tempering treatment, and after holding it for 1.5 hours, move it into the slow cooling pit and slowly cool it to room temperature to obtain the resistance Gri...
Embodiment 2
[0026] An impact-resistant steel ball for a ball mill, the weight percentage of each component is as follows:
[0027] C: 0.8%; Si: 0.3%; Cr: 2.3%; Mn: 0.8%; Ni: 0.3%; Ti: 0.06%; Al: 1.2%; W: 0.1%; Mo: 0.25%; S: 0.02%; P: 0.06%; the remainder is Fe;
[0028] During the preparation process, the impact-resistant steel balls for the ball mill were prepared according to the following process steps:
[0029] S1: Weigh the raw materials according to the weight percentage of each component for smelting, carry out refining in the refining device, and carry out final deoxidation in the later stage of refining, pouring, after casting and forming, cleaning to obtain castings;
[0030] S2: Keep the casting obtained in S1 at 870°C for 2.5 hours, then quench it in water, raise the temperature of the quenched casting to 260°C for tempering treatment, and after holding it for 1 hour, move it into the slow cooling pit and slowly cool it to room temperature to obtain the resistance Grinding s...
Embodiment 3
[0032] An impact-resistant steel ball for a ball mill, the weight percentage of each component is as follows:
[0033] C: 0.6%; Si: 0.2%; Cr: 1.5%; Mn: 0.6%; Ni: 0.2%; Ti: 0.04%; Al: 0.6%; W: 0.05%; Mo: 0.15%; S: 0.005%; P: 0.01%; the remainder is Fe;
[0034] During the preparation process, the impact-resistant steel balls for the ball mill were prepared according to the following process steps:
[0035] S1: Weigh the raw materials according to the weight percentage of each component for smelting, carry out refining in the refining device, and carry out final deoxidation in the later stage of refining, pouring, after casting and forming, cleaning to obtain castings;
[0036] S2: Keep the casting obtained in S1 at 850°C for 3.5 hours, then quench it in water, raise the temperature of the quenched casting to 240°C for tempering treatment, and after holding it for 2 hours, move it into the slow cooling pit and slowly cool it to room temperature to obtain the resistance Grindin...
PUM
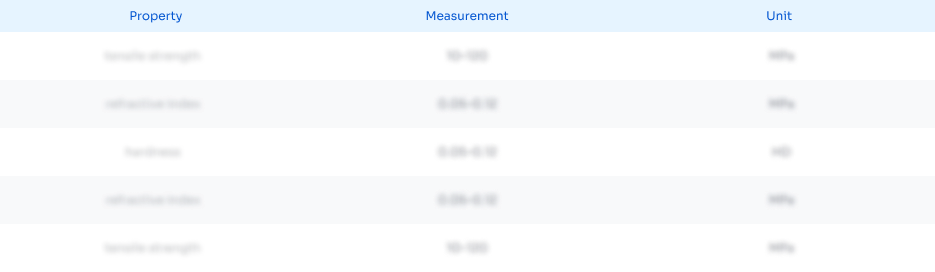
Abstract
Description
Claims
Application Information

- R&D Engineer
- R&D Manager
- IP Professional
- Industry Leading Data Capabilities
- Powerful AI technology
- Patent DNA Extraction
Browse by: Latest US Patents, China's latest patents, Technical Efficacy Thesaurus, Application Domain, Technology Topic, Popular Technical Reports.
© 2024 PatSnap. All rights reserved.Legal|Privacy policy|Modern Slavery Act Transparency Statement|Sitemap|About US| Contact US: help@patsnap.com