A Cooling System for Electric Spindle Core
A technology of cooling system and motorized spindle, applied in metal processing machinery parts, maintenance and safety accessories, metal processing equipment, etc., can solve the problem of heat dissipation of motorized spindle, stability and reliability problems, heat exchange power of heat pipe, etc. that cannot be effectively solved. limited and other problems, to achieve the effect of efficient and reliable cooling structure, low design and development cost, simple and efficient system equipment
- Summary
- Abstract
- Description
- Claims
- Application Information
AI Technical Summary
Problems solved by technology
Method used
Image
Examples
Embodiment Construction
[0024] Below in conjunction with accompanying drawing, the present invention is described in further detail:
[0025] Reference attached figure 1 and 2 , an electric spindle core cooling system of the present invention, a plurality of U-shaped cooling units 12 composed of straight-hole micro-channels are processed on the electric-spindle core 6, and the diameter of the straight-hole micro-channels is less than or equal to 3mm. A single U-shaped cooling unit 12 is composed of an inflow channel 5 , a return flow channel 8 and a connecting channel 7 located at the shaft core of the electric spindle near the front bearing. The processing position of the connecting channel 7 of a single U-shaped cooling unit 12 should avoid the interference fit between the inner ring of the front bearing and the shaft core 6 of the electric spindle. The connecting channel 7 is sealed by a plug 13 . The inlet of the inflow channel 5 and the outlet of the return channel 8 of each U-shaped cooling ...
PUM
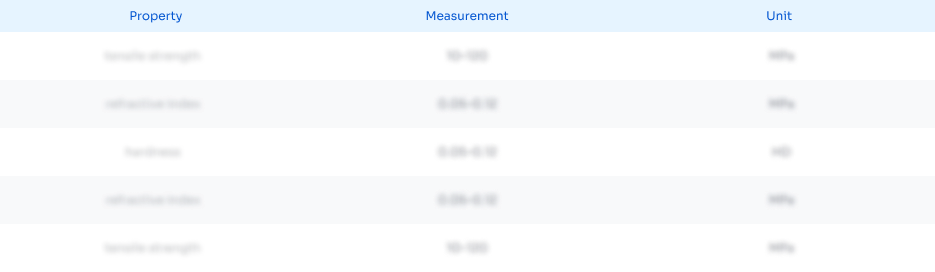
Abstract
Description
Claims
Application Information

- Generate Ideas
- Intellectual Property
- Life Sciences
- Materials
- Tech Scout
- Unparalleled Data Quality
- Higher Quality Content
- 60% Fewer Hallucinations
Browse by: Latest US Patents, China's latest patents, Technical Efficacy Thesaurus, Application Domain, Technology Topic, Popular Technical Reports.
© 2025 PatSnap. All rights reserved.Legal|Privacy policy|Modern Slavery Act Transparency Statement|Sitemap|About US| Contact US: help@patsnap.com