Method of manufacturing high-aperture ratio fine printed circuit board
A manufacturing method and technology of aperture ratio, applied in printed circuit manufacturing, printed circuits, electrical components, etc., can solve the problems of line shedding, increased side etching, uneven surface copper, etc., to avoid uneven surface copper, change etching, etc. The amount of side etching and the effect of reducing the difficulty of etching
- Summary
- Abstract
- Description
- Claims
- Application Information
AI Technical Summary
Problems solved by technology
Method used
Examples
Embodiment Construction
[0020] The present invention will be described in detail below in conjunction with specific embodiments.
[0021] A method for manufacturing a high-aperture-ratio fine-density circuit board, comprising the following steps:
[0022] (1) Made into multi-layer board: non-HDI board, board thickness ≤ 2.0mm, A / R> 6, outer circuit design is 3 / 3mil;
[0023] (2) drilling;
[0024] (3) Porous (PTH): After the hole is metallized, the whole board is not electroplated;
[0025] (4) The first graphics transfer: paste the graphics transfer dry film on the surface of the substrate, only transfer the graphics of all the metallized holes in the board, and do not transfer the required lines;
[0026] (5) Electroplating: the thickness of the hole copper is controlled at 0.4-0.6mil;
[0027] (6) Grinding: remove the pattern transfer dry film, and polish the protruding pads at the flat hole;
[0028] (7) The second graphics transfer: perform normal graphics transfer, that is, transfer the req...
PUM
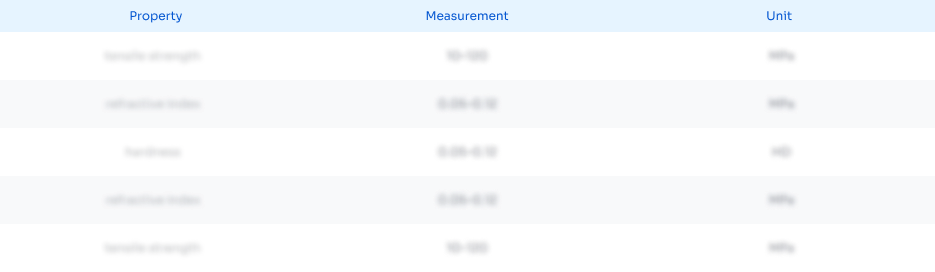
Abstract
Description
Claims
Application Information

- R&D
- Intellectual Property
- Life Sciences
- Materials
- Tech Scout
- Unparalleled Data Quality
- Higher Quality Content
- 60% Fewer Hallucinations
Browse by: Latest US Patents, China's latest patents, Technical Efficacy Thesaurus, Application Domain, Technology Topic, Popular Technical Reports.
© 2025 PatSnap. All rights reserved.Legal|Privacy policy|Modern Slavery Act Transparency Statement|Sitemap|About US| Contact US: help@patsnap.com