Wear-resisting rubber material for tires
A rubber material and tire technology, applied in the field of tire rubber materials, can solve the problems of unfavorable long-term use of tires, lack of comprehensive promotion and use, and high price of natural rubber, and achieve the effects of excellent anti-aging performance, improved wear resistance and low price.
- Summary
- Abstract
- Description
- Claims
- Application Information
AI Technical Summary
Problems solved by technology
Method used
Examples
Embodiment 1
[0016] A kind of wear-resistant tire rubber material proposed by the present invention, its raw material comprises by weight: 50 parts of styrene-butadiene rubber, 10 parts of butadiene rubber, 15 parts of natural rubber, 20 parts of isoprene rubber, 0.8 part of sulfur powder, accelerator NOBS2 1.7 parts of accelerator DM, 0.5 parts of accelerator TMTM, 15 parts of nanocellulose whiskers, 10 parts of barite powder, 23 parts of calcite powder, 7 parts of brucite powder, 8 parts of aluminum nitride, carbon black N23430 1.2 parts of monoalkoxy titanate coupling agent, 1 part of plasticizer DCHP, 7 parts of epoxy octyl stearate, 2640.3 parts of anti-aging agent, 2 parts of anti-aging agent MB;
[0017] In the preparation process, first mix the plasticizer DCHP and monoalkoxy titanate coupling agent evenly, then add nano-cellulose whiskers, barite powder, calcite powder, brucite powder and aluminum nitride at 52rpm Stir at a rotating speed of 11.6min to obtain mixed auxiliary mater...
Embodiment 2
[0019] A kind of wear-resistant tire rubber material that the present invention proposes, its raw material comprises by weight: 47 parts of styrene-butadiene rubber, 13 parts of high-cis butadiene rubber, 13 parts of natural rubber, 24 parts of isoprene rubber, 0.6 part of sulfur powder, 2.8 parts of accelerator NOBS, 1.5 parts of accelerator DM, 0.8 parts of accelerator TMTM, 12 parts of nanocellulose whiskers, 14 parts of barite powder, 22 parts of calcite powder, 8 parts of brucite powder, 7 parts of aluminum nitride Parts, 33 parts of carbon black N2343, 1.1 parts of monoalkoxy titanate coupling agent, 1.1 parts of plasticizer DCHP, 4 parts of epoxy octyl stearate, 2640.9 parts of anti-aging agent, 1.2 parts of anti-aging agent MB;
[0020] In the preparation process, after mixing the plasticizer DCHP and the monoalkoxy titanate coupling agent evenly, add nano-cellulose whiskers, barite powder, calcite powder, brucite powder and aluminum nitride at 55rpm Stir at the speed ...
Embodiment 3
[0022] A kind of wear-resistant tire rubber material proposed by the present invention, its raw material comprises by weight: 45 parts of styrene-butadiene rubber, 15 parts of butadiene rubber, 10 parts of natural rubber, 25 parts of isoprene rubber, 0.5 part of sulfur powder, accelerator NOBS3 1.3 parts of accelerator DM, 0.9 parts of accelerator TMTM, 10 parts of nanocellulose whiskers, 15 parts of barite powder, 20 parts of calcite powder, 9 parts of brucite powder, 5 parts of aluminum nitride, carbon black N23435 1 part, 1 part of monoalkoxy titanate coupling agent, 1.2 parts of plasticizer DCHP, 3 parts of epoxy octyl stearate, 2641.2 parts of anti-aging agent, 1 part of anti-aging agent MB;
[0023] In the preparation process, first mix the plasticizer DCHP and monoalkoxy titanate coupling agent evenly, then add nano-cellulose whiskers, barite powder, calcite powder, brucite powder and aluminum nitride at 50rpm Stir at the rotating speed of 12min to obtain mixed auxiliar...
PUM
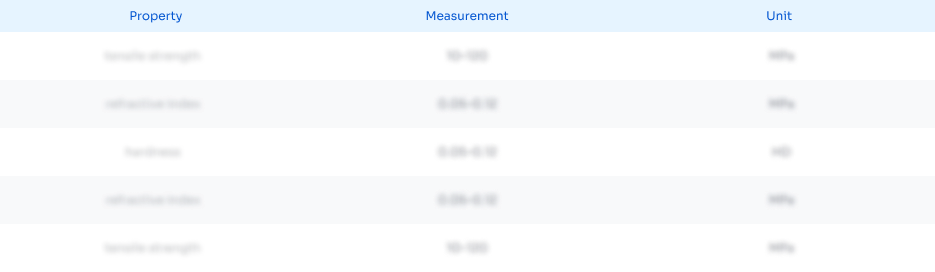
Abstract
Description
Claims
Application Information

- R&D
- Intellectual Property
- Life Sciences
- Materials
- Tech Scout
- Unparalleled Data Quality
- Higher Quality Content
- 60% Fewer Hallucinations
Browse by: Latest US Patents, China's latest patents, Technical Efficacy Thesaurus, Application Domain, Technology Topic, Popular Technical Reports.
© 2025 PatSnap. All rights reserved.Legal|Privacy policy|Modern Slavery Act Transparency Statement|Sitemap|About US| Contact US: help@patsnap.com