Synthesis method of ethyl gallate
A technology of ethyl gallate and a synthesis method, which is applied in the field of synthesis of ethyl gallate, can solve the problems of low yield rate of finished products, influence on the conversion rate of gallic acid, and high product cost, so as to achieve improved conversion rate and stable and reliable production process , The effect of cost reduction
- Summary
- Abstract
- Description
- Claims
- Application Information
AI Technical Summary
Problems solved by technology
Method used
Image
Examples
Embodiment 1
[0016] ①Add 100g of gallic acid, 500ml of anhydrous alcohol, and 10g of catalyst concentrated sulfuric acid into a three-necked flask; connect the constant pressure dropping funnel in turn (200g of water-absorbing molecular sieves are installed inside, and the molecular sieves are 3A molecular sieves, which must be dried in a drying oven to Anhydrous), rectification column (installed with glass filler), condensation pipe (through cooling water), thermometer (kettle temperature is controlled at 85-90°C, top temperature is controlled at 80-85°C), and electric heating with magnetic stirring Cover with heat (outside the three-necked flask), and react for 10 hours. (For the esterification reaction device, see the instruction manual figure 1 ).
[0017] ② After the reaction, distill the excess alcohol to recover 430 ml of ethanol, add 500 ml of soft water to cool and crystallize.
[0018] ③Coarsely filter the crude filtrate after 24 hours of crystallization to obtain 144.5 g of ...
Embodiment 2
[0022] ① Add 200g of gallic acid, 1000ml of absolute alcohol, and 20g of catalyst concentrated sulfuric acid into a three-necked flask. Connect to the constant pressure dropping funnel (400 g of water-absorbing molecular sieve is installed inside, the molecular sieve is 3A molecular sieve, and must be dried in a drying oven until there is no water before use), the rectification tower (installed with glass filler), and the condenser tube (through Cooling water), thermometer (kettle temperature is controlled at 85-90°C, top temperature is controlled at 80-85°C), heated on a magnetic stirring electric heating mantle, and reacted for 10 hours.
[0023] ②After the reaction, distill the excess alcohol to recover 860 ml of ethanol, add 1000 ml of soft water to cool and crystallize.
[0024] ③Coarsely filter the crude filtrate after 24 hours of crystallization to obtain coarse crystals of ethyl gallate 289 g. ④Decolorize. Put 289 g of coarse crystals of ethyl gallate into a three-ne...
Embodiment 3
[0028] ①Add 300g of gallic acid, 1500ml of absolute alcohol, and 30g of catalyst concentrated sulfuric acid into a three-necked flask. Connect to the constant pressure dropping funnel (600 g of water-absorbing molecular sieves inside, the molecular sieve is 3A molecular sieve, and must be dried in a drying oven until there is no water before use), the rectification tower (installed with glass filler), and the condenser tube (through cooling water), thermometer (kettle temperature is controlled at 85-90°C, top temperature is controlled at 80-85°C), and heated on a magnetic stirring electric heating mantle, and reacted for 10 hours.
[0029] ② After the reaction, distill the excess alcohol to recover 1300 ml of ethanol, add 1500 ml of soft water to cool and crystallize.
[0030] ③The crude filtrate was crystallized for 24 hours and then coarsely filtered to obtain 434 g of coarse crystals of ethyl gallate
[0031] ④ Decolorization Put 434g of ethyl gallate coarse cryst...
PUM
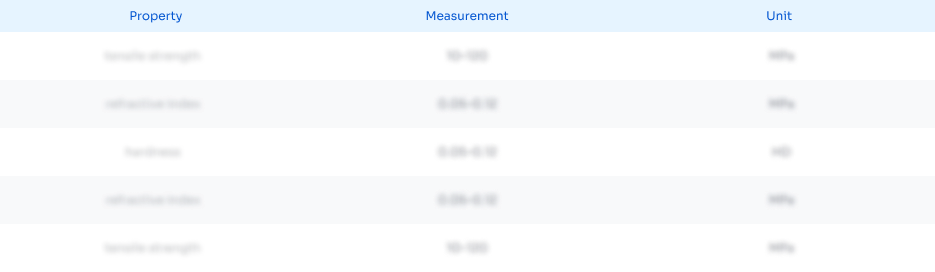
Abstract
Description
Claims
Application Information

- R&D
- Intellectual Property
- Life Sciences
- Materials
- Tech Scout
- Unparalleled Data Quality
- Higher Quality Content
- 60% Fewer Hallucinations
Browse by: Latest US Patents, China's latest patents, Technical Efficacy Thesaurus, Application Domain, Technology Topic, Popular Technical Reports.
© 2025 PatSnap. All rights reserved.Legal|Privacy policy|Modern Slavery Act Transparency Statement|Sitemap|About US| Contact US: help@patsnap.com