An energy recovery method for the process of producing propylene from oxygen-containing compounds
An energy recovery and compound technology, which is applied in the field of propylene production, can solve the problems of large heating furnace load, low energy utilization rate, and low overall energy efficiency level of the process, so as to deepen the heat exchange depth, improve the energy efficiency level of the process, and save energy. consumption effect
- Summary
- Abstract
- Description
- Claims
- Application Information
AI Technical Summary
Problems solved by technology
Method used
Image
Examples
Embodiment 1
[0023] In this embodiment, the feed is industrial methanol with a purity of 99.5%, and the methanol feed WHSV=2.0h -1 , using as figure 1 The process flow shown. The gas temperature at the inlet of reactor 5 is 450°C, the temperature of the reaction product after being compressed by the compressor is 600°C, and the pressure is 0.70MPa in gauge pressure. ℃, and then pass through the two-stage heat recovery unit of the methanol vaporizer and the circulating water preheater respectively. The temperature flowing out of the circulating water preheater is 130 ℃, and enters the air cooler to cool down to 30 ℃, and finally enters the phase separator to separate oil and water , gas three-phase. The water content in the outlet gas hydrocarbon product is 0.2wt%, and the water content in the oil phase product is 0.6wt%.
[0024] Through this scheme, the stream flowing out of the pre-reactor 3 is directly heated to 450° C. through a heat exchange to reach the reaction temperature of the...
Embodiment 2
[0028] In this embodiment, the feed is industrial methanol with a purity of 99.5%, and the methanol feed WHSV=1.0h -1 , using as figure 1 The process flow shown. The gas temperature at the inlet of reactor 5 is 400°C, the temperature of the reaction product after being compressed by the compressor is 550°C, and the pressure is 0.60MPa in gauge pressure. ℃, and then pass through the two-stage heat recovery unit of the methanol vaporizer and the circulating water preheater respectively. The temperature flowing out of the circulating water preheater is 110 ℃, and enters the air cooler to cool down to 40 ℃, and finally enters the phase separator to separate oil and water , gas three-phase. The water content in the outlet gas hydrocarbon product is 0.3wt%, and the water content in the oil phase product is 0.7wt%.
[0029] Through this solution, the stream flowing out of the pre-reactor 3 is directly heated to 400° C. through a heat exchange to reach the reaction temperature of t...
Embodiment 3
[0033] In this embodiment, the feed is industrial methanol with a purity of 99.5%, and the methanol feed WHSV=2.0h -1 , using as figure 1The process flow shown. The gas temperature at the inlet of reactor 5 is 380°C, the temperature of the reaction product after being compressed by the compressor is 530°C, and the pressure is 0.55MPa in gauge pressure. ℃, and then pass through the two-stage heat recovery unit of the methanol vaporizer and the circulating water preheater respectively. The temperature flowing out of the circulating water preheater is 100 ℃, and enters the air cooler to cool down to 40 ℃, and finally enters the phase separator to separate oil and water , gas three-phase. The water content in the outlet gas hydrocarbon product is 0.35wt%, and the water content in the oil phase product is 0.72wt%.
[0034] Through this solution, the stream flowing out of the pre-reactor 3 is directly heated to 380° C. through a heat exchange to reach the reaction temperature of ...
PUM
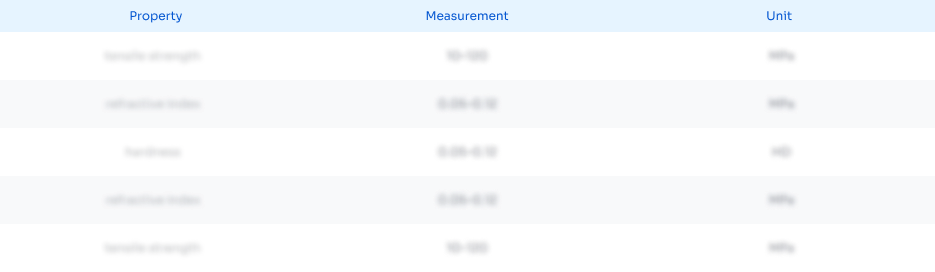
Abstract
Description
Claims
Application Information

- R&D
- Intellectual Property
- Life Sciences
- Materials
- Tech Scout
- Unparalleled Data Quality
- Higher Quality Content
- 60% Fewer Hallucinations
Browse by: Latest US Patents, China's latest patents, Technical Efficacy Thesaurus, Application Domain, Technology Topic, Popular Technical Reports.
© 2025 PatSnap. All rights reserved.Legal|Privacy policy|Modern Slavery Act Transparency Statement|Sitemap|About US| Contact US: help@patsnap.com