Preparation method for PDMS (polydimethylsiloxane)/PTFE polytetrafluoroethylene pervaporation hollow-fiber membrane
A technology of pervaporation and fiber membrane, applied in chemical instruments and methods, semi-permeable membrane separation, membrane technology, etc., can solve the problems of expensive materials, poor stability, etc., and achieve good selectivity, good support strength, and convenient operation Effect
- Summary
- Abstract
- Description
- Claims
- Application Information
AI Technical Summary
Problems solved by technology
Method used
Image
Examples
Embodiment 1
[0012] Dissolve 10g of polydimethylsiloxane (PDMS) in 100g of n-hexane, add 0.4g of cross-linking agent ethyl orthosilicate, mix and stir at room temperature for 0.5 hours, add 0.1g of catalyst dibutyltin dilaurate, add n-hexane alkane until the concentration of polydimethylsiloxane in the mixed solution is 5 wt%, and after sealing, stir at room temperature for 4 hours, and the obtained solution is centrifuged and defoamed to make a film-making solution. Rinse polytetrafluoroethylene (PTFE) hollow fiber membranes with distilled water until neutral, dry them at room temperature, and use them as base membranes. The treated basement membrane is immersed in the membrane-forming solution for 1-3 seconds, taken out, and dried at room temperature. Repeat the film coating 4 times, then put it into a vacuum oven and dry it under vacuum at 110°C for 12 hours until it is completely cross-linked to obtain a PDMS / PTFE composite hollow fiber membrane. The outer layer of the obtained compos...
Embodiment 2
[0017] Dissolve 20g of polydimethylsiloxane in 40g of n-hexane, add 1.5g of crosslinking agent ethyl orthosilicate, mix and stir at room temperature for 4 hours, then add 1.0g of catalyst dibutyltin dilaurate, add n-hexane to mix The concentration of polydimethylsiloxane in the liquid is 30wt%, and after being sealed, it is stirred at room temperature for 24 hours, and the obtained solution is centrifuged and defoamed to make a film-making liquid. Rinse the PTFE hollow fiber membrane with distilled water until neutral, dry it at room temperature, and use it as the base membrane. The treated basement membrane is immersed in the membrane-forming solution for 1-3 seconds, taken out, and dried at room temperature. Repeat the film coating once, then put it into a vacuum oven and dry it under vacuum at 50°C for 12 hours until it is completely cross-linked to obtain a PDMS / PTFE composite hollow fiber membrane. The outer layer of the obtained composite hollow fiber membrane is a dens...
Embodiment 3
[0022] Dissolve 20g of polydimethylsiloxane in 100g of n-hexane, add 1.5g of crosslinking agent ethyl orthosilicate, mix and stir at room temperature for 2 hours, then add 0.3g of catalyst dibutyltin dilaurate, add n-hexane until mixed The concentration of polydimethylsiloxane in the liquid is 15 wt%, and after being sealed, it is stirred at room temperature for 14 hours, and the obtained solution is centrifuged and defoamed to make a film-making liquid. Rinse the PTFE hollow fiber membrane with distilled water until neutral, dry it at room temperature, and use it as the base membrane. The treated basement membrane is immersed in the membrane-forming solution for 1-3 seconds, taken out, and dried at room temperature. The coating was repeated twice, and then placed in a vacuum oven at 90°C for 14 hours in a vacuum until it was completely cross-linked to obtain a PDMS / PTFE composite hollow fiber membrane. The outer layer of the obtained composite hollow fiber membrane is a dens...
PUM
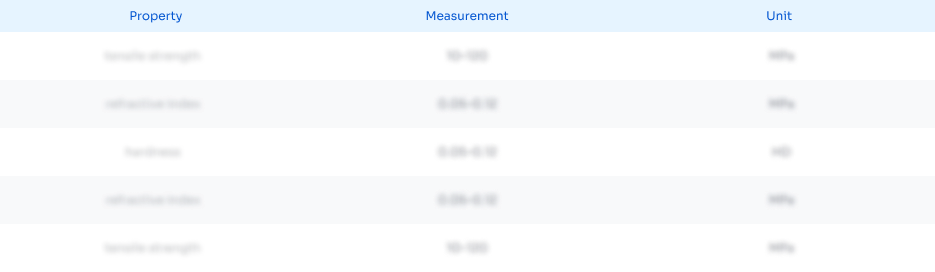
Abstract
Description
Claims
Application Information

- R&D
- Intellectual Property
- Life Sciences
- Materials
- Tech Scout
- Unparalleled Data Quality
- Higher Quality Content
- 60% Fewer Hallucinations
Browse by: Latest US Patents, China's latest patents, Technical Efficacy Thesaurus, Application Domain, Technology Topic, Popular Technical Reports.
© 2025 PatSnap. All rights reserved.Legal|Privacy policy|Modern Slavery Act Transparency Statement|Sitemap|About US| Contact US: help@patsnap.com