Method and system for field application and calibration of reflection fiber optic displacement sensor
A technology of displacement sensors and sensors, which is applied in the direction of instruments, optical devices, measuring devices, etc., can solve problems such as inability to establish on-site calibration, and achieve the effect of increasing accuracy, good stability and accuracy
- Summary
- Abstract
- Description
- Claims
- Application Information
AI Technical Summary
Problems solved by technology
Method used
Image
Examples
Embodiment 1
[0053] As shown in Figure 1, it is a method for on-site application calibration of a reflective optical fiber displacement sensor described in Embodiment 1 of the present application, which is applied to a calibration workbench including a target surface, a laser displacement sensor, an optical fiber displacement sensor and a motor on, including:
[0054] Step 101 , when it is detected that the target surface is within the measuring range of the laser displacement sensor and the optical fiber displacement sensor, a predetermined moving speed, a predetermined moving distance and a predetermined moving direction of the target surface are set.
[0055] In the process of calibration measurement, if only one sensor is used for calibration, a sensor with a higher resolution or at least in the same order of magnitude is required as a calibration reference. Although the reading of the spiral micrometer can be used as the reference displacement value of the optical fiber displacement d...
Embodiment 2
[0069] For the on-site calibration method of the reflective optical fiber displacement sensor described in the first embodiment above, it is necessary to set up a corresponding calibration workbench, such as image 3 As shown, among them,
[0070] For this embodiment, the calibration performed by the optical fiber displacement sensor requires a workbench with high rigidity and stable structure. The calibration table is composed of optical fiber displacement sensor bracket, laser displacement sensor bracket, reflective target surface, pulse stepping motor and table, such as image 3 As shown, the optical paths of the laser displacement sensor and the optical fiber displacement sensor are kept parallel, the support is stable, and various materials to be calibrated can be installed on the reflective target surface. The surface properties of the material must be consistent with the application, and the target surface is perpendicular to the optical path of the sensor. The stepper...
Embodiment 3
[0084] Such as Image 6 As shown, it is a system for on-site application calibration of a reflective optical fiber displacement sensor described in Embodiment 3 of the present application, which is applied to a calibration workbench including a target surface, a laser displacement sensor, an optical fiber displacement sensor and a motor, including : a preprocessing unit 601, a drive processing unit 602, a measurement processing unit 603, and a rendering unit 604; wherein,
[0085] The preprocessing unit 601 is coupled with the drive processing unit 602, and is used to set the predetermined moving speed and predetermined moving distance of the target surface when it is detected that the target surface is within the range of the laser displacement sensor and the optical fiber displacement sensor and the intended direction of movement.
[0086] In the process of calibration measurement, if only one sensor is used for calibration, a sensor with a higher resolution or at least in ...
PUM
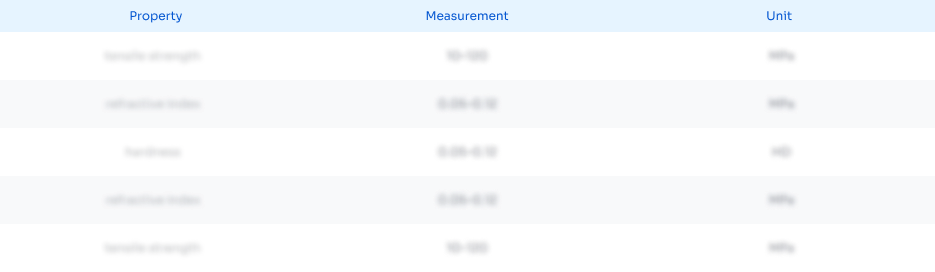
Abstract
Description
Claims
Application Information

- R&D
- Intellectual Property
- Life Sciences
- Materials
- Tech Scout
- Unparalleled Data Quality
- Higher Quality Content
- 60% Fewer Hallucinations
Browse by: Latest US Patents, China's latest patents, Technical Efficacy Thesaurus, Application Domain, Technology Topic, Popular Technical Reports.
© 2025 PatSnap. All rights reserved.Legal|Privacy policy|Modern Slavery Act Transparency Statement|Sitemap|About US| Contact US: help@patsnap.com